Difference between revisions of "Wave energy converters"
Dronkers J (talk | contribs) |
Dronkers J (talk | contribs) |
||
Line 1: | Line 1: | ||
==Introduction== | ==Introduction== | ||
− | Vast and reliable, wave power has long been considered as one of the most promising renewable energy sources. In a special IPCC 2011 report<ref name=IPCC>Lewis, A., Estefen, S., Huckerby, J., Musial, W., Pontes, T. and Torres-Martinez, J. 2011. Ocean Energy. In IPCC Special Report on Renewable Energy Sources and Climate Change Mitigation [O. Edenhofer, R. Pichs-Madruga, Y. Sokona, K. Seyboth, P. Matschoss, S. Kadner, T. Zwickel, P. Eickemeier, G. Hansen, S. Schlömer, C. von Stechow (eds)], Cambridge University Press, Cambridge, United Kingdom and New York, NY, USA.</ref> several estimates are presented for the world total potential of ocean wave energy resources. These estimates were obtained using methods as illustrated in | + | Vast and reliable, wave power has long been considered as one of the most promising renewable energy sources. In a special IPCC 2011 report<ref name=IPCC>Lewis, A., Estefen, S., Huckerby, J., Musial, W., Pontes, T. and Torres-Martinez, J. 2011. Ocean Energy. In IPCC Special Report on Renewable Energy Sources and Climate Change Mitigation [O. Edenhofer, R. Pichs-Madruga, Y. Sokona, K. Seyboth, P. Matschoss, S. Kadner, T. Zwickel, P. Eickemeier, G. Hansen, S. Schlömer, C. von Stechow (eds)], Cambridge University Press, Cambridge, United Kingdom and New York, NY, USA.</ref> several estimates are presented for the world total potential of ocean wave energy resources. These estimates were obtained using methods as illustrated in Appendix A. The theoretical maximum has been estimated at about 30,000 TWh/yr (3.10<sup>13</sup> kWh/yr), which is about 20% of the 2019 world energy consumption. However, given technological and economic constraints, the exploitable resource is probably almost a factor 10 less. |
− | Wave Energy Converters (WECs) convert wave power into electricity. Although attempts to utilize this resource date back to at least 1890, wave power is currently not widely employed | + | Wave Energy Converters (WECs) convert wave power into electricity. Although attempts to utilize this resource date back to at least 1890, wave power is currently not widely employed<ref>Miller, C. 2004. A Brief History of Wave and Tidal Energy Experiments in San Francisco and Santa Cruz. [http://www.outsidelands.org/wave-tidal.php]</ref>. The operational wave power installed worldwide in 2020 totaled approximately 16 MW [https://www.weamec.fr/en/synthesis/ocean-energy-key-trends-and-statistics-2019/], which is about 5 orders of magnitude less than the 2-3 TW required to exploit the global wave energy potential. An important reason is the production costs per kWh, which were in 2020 about a factor 10 higher compared to offshore wind farms <ref>IRENA, 2014. Ocean Energy Technology Brief 4, www.irena.org</ref>. |
− | A plethora of innovational methods for wave power conversion have been invented in the last three decades, resulting in thousands of patents over recent years. At present, a number of different wave energy concepts are being investigated by companies and academic research groups around the world. Although many working designs have been developed and tested through modelling and wave tank-tests, only a few concepts have progressed to sea testing. Strong cost reductions, which are only possible with a sharp increase in global application, should enable wave plants to compete favorably with conventional power plants in the | + | A plethora of innovational methods for wave power conversion have been invented in the last three decades, resulting in thousands of patents over recent years. At present, a number of different wave energy concepts are being investigated by companies and academic research groups around the world. Although many working designs have been developed and tested through modelling and wave tank-tests, only a few concepts have progressed to sea testing. Strong cost reductions, which are only possible with a sharp increase in global application, should enable wave plants to compete favorably with conventional power plants in the future<ref>Pelc, R. and Fujita, R.M. 2002. Renewable energy from the ocean. Marine Policy, 26: 471-479.</ref>. |
==Wave Energy Conversion Principles== | ==Wave Energy Conversion Principles== | ||
− | In this section the most popular current methods for wave energy conversion are briefly presented. | + | In this section the most popular current methods for wave energy conversion are briefly presented. An indication of the efficiency of these methods is presented in Appendix B. |
===Oscillating Water Columns=== | ===Oscillating Water Columns=== | ||
Line 15: | Line 15: | ||
[[File:REWEC.jpg|thumb|left|500px|Fig. 1. Wave energy conversion using the principle of the oscillating water column. From IPCC 2011<ref name=IPCC/>.]] | [[File:REWEC.jpg|thumb|left|500px|Fig. 1. Wave energy conversion using the principle of the oscillating water column. From IPCC 2011<ref name=IPCC/>.]] | ||
− | The principle of the oscillating water column is illustrated in Fig. 1, in this example for use in conjunction with a fixed structure (e.g., breakwater). The functioning of the oscillating water columns (OWCs) is | + | The principle of the oscillating water column is illustrated in Fig. 1, in this example for use in conjunction with a fixed structure (e.g., breakwater). The functioning of the oscillating water columns (OWCs) is somewhat similar to that of a wind turbine, being based on the principle of wave induced air pressurization. The device is set upon a closed air chamber, which is placed above the water. The passage of waves changes the water level within the closed housing and the rising and falling water level increases and decreases the air pressure within the housing introducing a bidirectional air flow. By placing a turbine on top of this chamber air will pass in and out of it with the changing air pressure levels. |
− | [[File:WellsTurbine.jpg|thumb|right|150px|Fig. 2. Wells turbine. From<ref name=FH>Falcao, F.O. and Henriques, J.C.C. 2016. Oscillating-water-column wave energy converters and air turbines: A review. Renewable Energy 85:1391-1424</ref>).]] | + | [[File:WellsTurbine.jpg|thumb|right|150px|Fig. 2. Wells turbine. From<ref name=FH>Falcao, F.O. and Henriques, J.C.C. 2016. Oscillating-water-column wave energy converters and air turbines: A review. Renewable Energy 85: 1391-1424</ref>).]] |
− | There are two options to separate the bi-directional flow: a [https://en.wikipedia.org/wiki/Wells_turbine Wells turbine] to create suction or alternatively, pressure generating valves | + | There are two options to separate the bi-directional flow: a [https://en.wikipedia.org/wiki/Wells_turbine Wells turbine] to create suction or alternatively, pressure generating valves<ref>Kofoed, J.P. and Frigaard, P., 2008. Hydraulic evaluation of the LEANCON wave energy converter. ''DCE Technical Report No. 45''. Dep. of Civil Eng., Aalborg University, Oct. 2008. Leancon Wave Energy. [http://www.leancon.com/ Leancon website]</ref>. The Wells turbine is constructed such that it rotates always in the same direction regardless of airflow direction, see Fig. 2. The efficiency is lower (50-60%) than with conventional turbines, but higher than achievable with conventional turbines in alternating mode<ref name=D9>Drew, B., Plummer, A.R. and Sahinkaya, M.N. 2009. A review of wave energy converter technology. Proceedings of the Institution of Mechanical Engineers, Part A: Journal of Power and Energy 223(8): 887-902</ref>. |
{| border="0" align="left" | {| border="0" align="left" | ||
Line 32: | Line 32: | ||
− | Special buoys have been developed for the application of OWC converters in deep water, according to the principle of Fig. 3. The length of the shaft determines the resonance frequency, allowing optimum energy efficiency to be achieved. An example of an offshore OWC is the Spar Buoy, Fig. 4. The original concept was invented by Yoshio Masuda (1925-2009), who developed navigation buoys powered by wave energy, equipped with an air turbine. It is circular in plane and therefore invariant to wave direction (Fig. 4). The size varies according to the target sea conditions at the deployment site but maximum dimensions were estimated at | + | Special buoys have been developed for the application of OWC converters in deep water, according to the principle of Fig. 3. The length of the shaft determines the resonance frequency, allowing optimum energy efficiency to be achieved. An example of an offshore OWC is the Spar Buoy, Fig. 4. The original concept was invented by Yoshio Masuda (1925-2009), who developed navigation buoys powered by wave energy, equipped with an air turbine. It is circular in plane and therefore invariant to wave direction (Fig. 4). The size varies according to the target sea conditions at the deployment site but maximum dimensions were estimated at 30 m diameter, 50 m height and 35 m draft, which could deliver up to 450 kW. |
<br clear=all> | <br clear=all> | ||
[[Image:WaveDragon.jpg|thumb|right|300px|Figure 5: Wave Dragon overtopping wave energy converter. ]] | [[Image:WaveDragon.jpg|thumb|right|300px|Figure 5: Wave Dragon overtopping wave energy converter. ]] | ||
===Overtopping Devices=== | ===Overtopping Devices=== | ||
− | Another type of wave energy converter is the overtopping device, which | + | Another type of wave energy converter is the overtopping device, which operates somewhat similar to a hydroelectric dam. The "Wave Dragon" created by Wave Dragon ApS<ref>Wave Dragon ApS [http://www.wavedragon.net/ Wave Dragon website]</ref> is the best known example of an offshore overtopping device (Fig. 5). Its floating arms focus waves onto a slope from which the wave overtops into a reservoir. The resulting difference in water elevation between the reservoir and the mean sea level then drives low-head hydro turbines. It was estimated that an optimal size design of 260 m width and 150 m length can produce up to 4 MW. In wave climates above 33 kW/m, this technology was expected to be economically competitive with offshore wind power in the near future. After a combined cost saving and power efficiency increase, the power price could eventually be in line with costs of fossil fuel generation<ref>Christensen, L., Friis-Madsen, E., Kofoed, J.P., 2005. The Wave Energy Challenge: The Wave Dragon case. ''PowerGen 2005 Europe Conference - Wave Dragon'', 20pp.</ref>. However, a feasibility study for a Wave Dragon deployment at the northern Spanish coast published in 2020 reported costs which were still a factor 10 higher<ref>Castro-Santos, L., Bento, A.R. and Soares, C.G. 2020. The Economic Feasibility of Floating Offshore Wave Energy Farms in the North of Spain. Energies 13, 806; doi:10.3390/en13040806</ref>. |
Near the shore, overtopping converters can be installed in front of or as part of caisson breakwaters. An example is the SeaWave Slot-Cone Generator (SSG)<ref>Vicinanza, D., Margheritini, L., Kofoed, J.P. and Buccino, M. 2012.The SSG Wave Energy Converter: Performance, Status and Recent Developments. Energies 5: 193-226</ref>, which collects seawater by wave overtopping over several reservoirs placed above each other, resulting in high hydraulic efficiency, see [[Wave energy converters in coastal structures]]. | Near the shore, overtopping converters can be installed in front of or as part of caisson breakwaters. An example is the SeaWave Slot-Cone Generator (SSG)<ref>Vicinanza, D., Margheritini, L., Kofoed, J.P. and Buccino, M. 2012.The SSG Wave Energy Converter: Performance, Status and Recent Developments. Energies 5: 193-226</ref>, which collects seawater by wave overtopping over several reservoirs placed above each other, resulting in high hydraulic efficiency, see [[Wave energy converters in coastal structures]]. | ||
Line 44: | Line 44: | ||
A great number of different devices have been developed to harness wave energy directly by using wave-induced water motion. The most popular types are displayed schematically in Fig. 6. | A great number of different devices have been developed to harness wave energy directly by using wave-induced water motion. The most popular types are displayed schematically in Fig. 6. | ||
− | [[File:WaveAbsorbers.jpg|thumb|center|700px|Fig. 6. Different energy conversion principles based on absorption of wave energy. Image from <ref>Hansen, R.H., Kramer, M.M. and Vidal, E. 2013. Discrete Displacement Hydraulic Power Take-Off System for the Wavestar Wave Energy Converter. Energies 6: 4001-4044; doi:10.3390/en6084001</ref> www.mdpi.com/journal/energies Creative Commons licence.]] | + | [[File:WaveAbsorbers.jpg|thumb|center|700px|Fig. 6. Different energy conversion principles based on absorption of wave energy. Image from <ref>Hansen, R.H., Kramer, M.M. and Vidal, E. 2013. Discrete Displacement Hydraulic Power Take-Off System for the Wavestar Wave Energy Converter. Energies 6: 4001-4044; doi:10.3390/en6084001</ref> https://www.mdpi.com/journal/energies Creative Commons licence.]] |
====Point absorbers==== | ====Point absorbers==== | ||
− | [[Image:Point absorbers and attenuators.jpg|thumb|right|250px|Figure 7 | + | [[Image:Point absorbers and attenuators.jpg|thumb|right|250px|Figure 7. The FO3 point absorber (top) and the Wave Star attenuator (bottom)]] |
− | Point absorber are buoy-type wave energy converters (WECs) that harvest incoming wave-energy from all directions. They are placed offshore at the ocean surface or just below. A vertically submerged floater absorbs wave energy which is converted by a piston or linear generator into electricity. One such a point absorber WEC is the FO3 concept developed by Norwegian entrepreneur Fred Olsen. It consists of several (12 or 21) heaving floaters attached to a 36 by 36 meter rig (Fig. 7). By means of a hydraulic system, the vertical motion is converted into a rotational movement that drives the hydraulic motor. This motor in turn powers the generator that can produce up to 2,52 MW | + | Point absorber are buoy-type wave energy converters (WECs) that harvest incoming wave-energy from all directions. They are placed offshore at the ocean surface or just below. A vertically submerged floater absorbs wave energy which is converted by a piston or linear generator into electricity. One such a point absorber WEC is the FO3 concept developed by Norwegian entrepreneur Fred Olsen. It consists of several (12 or 21) heaving floaters attached to a 36 by 36 meter rig (Fig. 7 top). By means of a hydraulic system, the vertical motion is converted into a rotational movement that drives the hydraulic motor. This motor in turn powers the generator that can produce up to 2,52 MW<ref>Leirbukt, A. and Tubaas, P. 2006. A wave of renewable energy. ABB Review 3: 29-31</ref>. |
− | The multiple point absorber type WEC "Wave Star", developed by Wave Star ApS<ref>Wave Star ApS [http://wavestarenergy.com/ website]</ref>, has a number of floaters on movable arms (Fig. 7). The energy of the motion of the arms is again captured in a common hydraulic line and converted into electric current. Most noticeably, being able to raise the entire installation along its pillars, this system has a high endurance for rough storm conditions. So far, this method has not been deployed at full scale. A 1:2 scaled installation has been built at Hanstholm which turns out 600 kW. However, production is thought to be scale-able up to 6 MW | + | The multiple point absorber type WEC "Wave Star", developed by Wave Star ApS<ref>Wave Star ApS [http://wavestarenergy.com/ website]</ref>, has a number of floaters on movable arms (Fig. 7 bottom). The energy of the motion of the arms is again captured in a common hydraulic line and converted into electric current. Most noticeably, being able to raise the entire installation along its pillars, this system has a high endurance for rough storm conditions. So far, this method has not been deployed at full scale. A 1:2 scaled installation has been built at Hanstholm which turns out 600 kW. However, production is thought to be scale-able up to 6 MW<ref>Bjerrum, A. 2008. Wave Energy - new unlimited source of energy. European Renewable Energy Conference presentation.</ref>. A major benefit of these types of exploitation is the minimal contact with water, placing any delicate machinery and electrics out of reach of any corrosion or physical forcing of the waves. The Wave Star development was abandoned in 2016. |
− | ==== | + | ====Terminators==== |
− | [ | + | Terminators consist of flaps that rotate with the wave orbital motion around an axis parallel to the wave front. Examples are the Oyster (Fig. 8a) and the [https://aw-energy.com/waveroller/ WaveRoller](Fig. 8b), both bottom-hinged terminators and the Salter Duck (Fig. 8c), with a rotation axis near the surface. Although these designs capture wave energy with a high efficiency (see Appendix B), no large-scale operational deployments have been realized. They are installed in intermediate depths, not far from the shore, where the wave front direction is most of the time close to shore-parallel. Oyster and WaveRoller have been tested in nature; for Salter Duck no full-scale prototype was built. Oyster’s electrical output is generated by an hydro-electric turbine onshore, driven by high pressure water via subsea pipelines. WaveRoller is equipped with an on board hydraulic system that drives an electricity generator, which is connected to the electric grid via a subsea cable. |
− | + | Hinged wave surge converters generally use hydraulic systems for power take-off. Hydraulic systems are well suited to harvest energy from high-force, slow-oscillatory motions which have to be converted to rotary motion and drive a generator. In order to rectify the fluctuating wave power, which would result in variable electrical power output unsuited to the electrical grid, some sort of energy storage system (or other means of compensation, such as an array of devices) is usually incorporated in the PTO system, such as accumulators, which can function as short term energy storage, helping the system handle the fluctuations<ref name=D9/>. | |
+ | |||
+ | {| border="0" align="center" | ||
+ | |- | ||
+ | | valign="top"| | ||
+ | [[File:OysterWEC.jpg|thumb|left|200px|Fig. 8a. Bottom-hinged wave energy converter Oyster.]] | ||
+ | | valign="top"| | ||
+ | [[File:WaveRollerWEC.jpg|thumb|left|200px|Fig. 8b. Bottom-hinged wave energy converter WaveRoller.]] | ||
+ | | valign="top"| | ||
+ | [[File:SalterDuckWEC.jpg|thumb|left|200px|Fig. 8c. Top-hinged wave energy converter Salter Duck.]] | ||
+ | |} | ||
+ | |||
+ | |||
+ | |||
+ | ====Wave attenuators==== | ||
+ | [[File:DEXAWEC.jpg|thumb|left|500px|Figure 9. DEXA wave energy converter and working principle.]] | ||
+ | The "DEXA", developed and patented by DEXA Wave Energy ApS <ref name="DEXA">Dexawave Energy ApS. [https://wavepartnership.dk/dexa-wave Dexawave website]</ref>, is an illustrative example of a wave attenuator. The device consists of two hinged catamarans that pivot relative to the other (Fig. 9). The resulting oscillatory flux at the hinge, is harnessed by means of a water-based low pressure power transmission that restrains angular oscillations. Flux generation is optimized by placing the floaters of each catamaran half a wavelength apart. A scaled prototype (dimensions 44x16.2m<ref name="Kofoed">Kofoed, J.P. 2009. Hydraulic evaluation of the DEXA wave energy converter. DCE Technical Report No. 57. Dep. of Civil Eng., Aalborg University, 23 pp.</ref>) placed in the Danish part of the North Sea should generate 160 kW<ref name="Martinelli">Martinelli L., Zanuttigh,B. and Kofoed, J.P. 2009. Statistical analysis of power production from OWC type wave energy converters. EWTEC Conference, Uppsala, 7-11 Sept 2009</ref>. Full-scale models are thought to be able to generate up to 250 kW<ref name="DEXA"/>. However, the DEXA development was terminated in 2012. | ||
− | |||
− | |||
==Power take-off systems (PTO)== | ==Power take-off systems (PTO)== | ||
The power take-off (PTO) system of a wave energy converter has a direct impact on the capital cost of a project by usually accounting for between 20 and 30% of the overall investment. The economic viability, efficiency and complexity of a wave energy converter depends largely on its PTO system. Maintenance at sea is a demanding and expensive task; high reliability and durability of all components of the PTO system are therefore required. This is technically challenging for systems exposed to the harsh marine environment, especially systems that consist of many moving parts that are exposed to corrosion and fouling. Several popular PTO systems have been reviewed by Ahamed et al. (2020<ref name=A20>Ahamed, R., McKee, K. and Howard, I. 2020. Advancements of wave energy converters based on power take off (PTO) systems: A review. Ocean Engineering 204, 107248</ref>), from which the summary below is extracted. | The power take-off (PTO) system of a wave energy converter has a direct impact on the capital cost of a project by usually accounting for between 20 and 30% of the overall investment. The economic viability, efficiency and complexity of a wave energy converter depends largely on its PTO system. Maintenance at sea is a demanding and expensive task; high reliability and durability of all components of the PTO system are therefore required. This is technically challenging for systems exposed to the harsh marine environment, especially systems that consist of many moving parts that are exposed to corrosion and fouling. Several popular PTO systems have been reviewed by Ahamed et al. (2020<ref name=A20>Ahamed, R., McKee, K. and Howard, I. 2020. Advancements of wave energy converters based on power take off (PTO) systems: A review. Ocean Engineering 204, 107248</ref>), from which the summary below is extracted. | ||
− | [[File:DirectElectricalDrive.jpg|thumb|150px|left|Fig. | + | [[File:DirectElectricalDrive.jpg|thumb|150px|left|Fig. 10. Schematic of a linear electrical generator based on a permanent magnet generator. Image from Ahamed et al. (2020<ref name=A20/>).]] |
− | Oscillating water column wave converters (OWC) generally use the previously described Wells turbine as PTO system. These turbines are vulnerable due to the relatively large number of moving parts. | + | Oscillating water column wave converters (OWC) generally use the previously described Wells turbine as PTO system. These turbines are vulnerable due to the relatively large number of moving parts. |
Overtopping devices are generally equipped with hydro turbines for power take-off. Conventional hydro turbines require for high efficiency more head and flow than provided by overtopping ocean waves. | Overtopping devices are generally equipped with hydro turbines for power take-off. Conventional hydro turbines require for high efficiency more head and flow than provided by overtopping ocean waves. | ||
Wave absorbing devices use hydraulic motor systems or direct mechanical or electrical drive PTO systems. Hydraulic motor-based PTO systems are suited for converting the low-speed oscillating motion into energy. However, the hydraulic motor-based PTO system consists of many mechanical moving parts and due to compression and decompression of the fluid there is a risk of hydraulic oil leakage. | Wave absorbing devices use hydraulic motor systems or direct mechanical or electrical drive PTO systems. Hydraulic motor-based PTO systems are suited for converting the low-speed oscillating motion into energy. However, the hydraulic motor-based PTO system consists of many mechanical moving parts and due to compression and decompression of the fluid there is a risk of hydraulic oil leakage. | ||
− | Direct mechanical drive uses linear-to-rotary conversion systems without pneumatic or hydraulic systems. The efficiency is high, but the lifetime is relatively short and maintenance costs are substantial. Direct electrical drive transmits the wave energy into electrical energy directly by coupling the mechanical energy to the moving part of a linear generator (Fig. | + | Direct mechanical drive uses linear-to-rotary conversion systems without pneumatic or hydraulic systems. The efficiency is high, but the lifetime is relatively short and maintenance costs are substantial. Direct electrical drive transmits the wave energy into electrical energy directly by coupling the mechanical energy to the moving part of a linear generator (Fig. 10). Issues are the need for a heavy structure due to the attractive forces between the stator and the translator and the complicated power transmission system due to the unequal generated voltage created by the irregular wave motion. |
− | The [https://en.wikipedia.org/wiki/Nanogenerator#Triboelectric_nanogenerator 'Triboelectric nanogenerator' (TENG)] and its extension, the 'Triboelectric−Electromagnetic Hybrid Nanogenerator' (TENG-EMG)<ref>Wen, Z., Guo, H., Zi, Y., Yeh, M.-H., Wang, X., Deng, J., Wang, J., Li, S., Hu, C. and Zhu, L. 2016. Harvesting broad frequency band blue energy by a triboelectric–electromagnetic hybrid nanogenerator. ACS Nano 10 (7): 6526–6534</ref>, are a new development that can efficiently harvest energy in any frequency range, are low-cost lightweight, easy to fabricate and easy to be scaled (size of individual units being below the micrometer scale). The nanogenerator uses a polymer-metal pair to create contact electrification ([https://en.wikipedia.org/wiki/Triboelectric_effect triboelectric effect]) between two materials sliding against each other and to induce charge transfer between their electrodes due to electrostatic induction, either in a layer structure or in a spherical-shell structure<ref name=H2020>Huang, B., Wang, P., Wang, L., Yang, S. and Wu, D. 2020. Recent advances in ocean wave energy harvesting by triboelectric nanogenerator: An overview Nanotechnology Reviews 9(1)</ref>, see Fig. | + | The [https://en.wikipedia.org/wiki/Nanogenerator#Triboelectric_nanogenerator 'Triboelectric nanogenerator' (TENG)] and its extension, the 'Triboelectric−Electromagnetic Hybrid Nanogenerator' (TENG-EMG)<ref>Wen, Z., Guo, H., Zi, Y., Yeh, M.-H., Wang, X., Deng, J., Wang, J., Li, S., Hu, C. and Zhu, L. 2016. Harvesting broad frequency band blue energy by a triboelectric–electromagnetic hybrid nanogenerator. ACS Nano 10 (7): 6526–6534</ref>, are a new development that can efficiently harvest energy in any frequency range, are low-cost lightweight, easy to fabricate and easy to be scaled (size of individual units being below the micrometer scale). The nanogenerator uses a polymer-metal pair to create contact electrification ([https://en.wikipedia.org/wiki/Triboelectric_effect triboelectric effect]) between two materials sliding against each other and to induce charge transfer between their electrodes due to electrostatic induction, either in a layer structure or in a spherical-shell structure<ref name=H2020>Huang, B., Wang, P., Wang, L., Yang, S. and Wu, D. 2020. Recent advances in ocean wave energy harvesting by triboelectric nanogenerator: An overview Nanotechnology Reviews 9(1)</ref>, see Fig. 11. Challenges for application in a prototype lie in the use of TENGs for power transfer to the shore, cost to scale, lifetime of the TENG materials in the ocean environment and connection methods of the thousands of TENG units that are needed. |
− | [[File:TENG.jpg|thumb|center|700px|Fig. | + | [[File:TENG.jpg|thumb|center|700px|Fig. 11. Principle of tribo-electric nanogenerators. (a) Triboelectric charges are generated on the surface of two laterally sliding dielectric films, due to frictional effects. Polarization occurring in the sliding plane drives an electron flow between the metal electrodes that generates an alternating current. (b) Soft contact rolling-mode spherical TENG (SS-TENG). When receiving external vibration from the ocean waves, the ball will roll back and forth between the electrodes to provide AC power to the external load. The soft ball maximizes the contact area. Images from Huang et al. (2020<ref name=H2020/>), Creative Commons licence.]] |
Line 77: | Line 91: | ||
To be able to produce energy at competitive prices, several obstacles have to be overcome. The following factors in particular determine the high costs of wind energy. | To be able to produce energy at competitive prices, several obstacles have to be overcome. The following factors in particular determine the high costs of wind energy. | ||
− | A very robust construction made of high quality materials is required that remains intact under severe storms and withstands the demanding conditions at sea, leading to corrosion, fouling and fatigue. The classical protection measure against fouling and corrosion of steel structures is regular maintenance and repainting. But this is time-consuming and costly because of the difficult access to offshore installations, especially under harsh conditions when damage occurs. In addition, the use of antifouling paints may be detrimental to the marine environment (e.g. Tributyltin paints<ref>Paul, J.D. and Davies, I.M. | + | A very robust construction made of high quality materials is required that remains intact under severe storms and withstands the demanding conditions at sea, leading to corrosion, fouling and fatigue. The classical protection measure against fouling and corrosion of steel structures is regular maintenance and repainting. But this is time-consuming and costly because of the difficult access to offshore installations, especially under harsh conditions when damage occurs. In addition, the use of antifouling paints may be detrimental to the marine environment (e.g. Tributyltin paints<ref>Paul, J.D. and Davies, I.M. 1986. Effects of copper- and tin-based anti-fouling compounds on the growth of scallops (Pecten maximus) and oysters (Crassostrea gigas). Aquaculture 54: 191-203</ref>). Full-scale devices out of concrete may provide a valuable alternative since concrete is long-lived if properly mixed<ref>Metha, P.K. 2001. Reducing the Environmental Impact of Concrete. Concrete International October 61-66</ref>. The cost of repairs is a major component of the wave farm costs. The reliability of the components, especially due to the cost of eventual repair actions, is pivotal for the economic viability of a project<ref name=R18>Rinaldi, G., Portillo, J.C.C., Khalid, F., Henriques, J.C.C., Thies, P.R., Gato, L.M.C. and Johanning, L. 2018. Multivariate analysis of the reliability, availability, and maintainability characterizations of a Spar–Buoy wave energy converter farm. Journal of Ocean Engineering and Marine Energy 4: 199–215</ref>. Deployments should be capable of lasting 30 years or more. This is a tall order as demonstrated by the mooring of the Wave Dragon that failed during a severe storm on the 8<sup>th</sup> of january 2004. |
The power generated by ocean waves fluctuates strongly due to the irregular wave climate, which makes connection to the electricity grid difficult<ref>Sjolte, J. 2014. Marine Renewable Energy Conversion: Grid and Off-Grid Modeling, Design and Operation. Doctoral Thesis, Norges Teknisk-Naturvitenskapelige Universitet, Trondheim, Norway</ref>. In addition, connection points to the electricity grid may not be available in areas where the conditions for wave energy generation are most favorable. | The power generated by ocean waves fluctuates strongly due to the irregular wave climate, which makes connection to the electricity grid difficult<ref>Sjolte, J. 2014. Marine Renewable Energy Conversion: Grid and Off-Grid Modeling, Design and Operation. Doctoral Thesis, Norges Teknisk-Naturvitenskapelige Universitet, Trondheim, Norway</ref>. In addition, connection points to the electricity grid may not be available in areas where the conditions for wave energy generation are most favorable. | ||
Line 83: | Line 97: | ||
Crucial for any design is the mooring which ensures a maintained position under both normal operating loads as well as extreme storm load conditions. It should not exert excess tension loads on the electrical transmission cables and ensure the suitable safety distances between devices in multiple installations. Most commonly, a free hanging catenary configuration is used for mooring but multi-catenary systems and flexible risers are not infrequent as well. Every configuration should be sufficiently compliant to accommodate tidal variations and environmental loading while remaining sufficiently stiff to allow berthing for inspections and maintenance. | Crucial for any design is the mooring which ensures a maintained position under both normal operating loads as well as extreme storm load conditions. It should not exert excess tension loads on the electrical transmission cables and ensure the suitable safety distances between devices in multiple installations. Most commonly, a free hanging catenary configuration is used for mooring but multi-catenary systems and flexible risers are not infrequent as well. Every configuration should be sufficiently compliant to accommodate tidal variations and environmental loading while remaining sufficiently stiff to allow berthing for inspections and maintenance. | ||
− | Due to the great variability of the wave climate with rare extremes, it is important to be able to test prototype designs over a long period before they are deployed on a large scale. Mathematical simulation models can be of great value here, because this is a quick and relatively inexpensive way to test a design for its effectiveness and efficiency at the long term, both in terms of capital and operational expenses, to achieve the lowest overall cost of electricity. For this purpose, the modeling tool supports the decision-maker in the pursuit of the most reliable and easy to maintain device design but also reports the trade-off between energetic yield and operational and maintenance efforts<ref name=R18/>. | + | Due to the great variability of the wave climate with rare extremes, it is important to be able to test prototype designs over a long period before they are deployed on a large scale. Mathematical simulation models can be of great value here, because this is a quick and relatively inexpensive way to test a design for its effectiveness and efficiency at the long term, both in terms of capital and operational expenses, in order to achieve the lowest overall cost of electricity. For this purpose, the modeling tool supports the decision-maker in the pursuit of the most reliable and easy to maintain device design but also reports the trade-off between energetic yield and operational and maintenance efforts<ref name=R18/>. |
The power take-off system is a crucial part of wave energy converters, which largely determines the cost, efficiency and reliability of the WEC. Many studies focus on optimisation of the PTOs; several challenges related to PTOs are mentioned in the previous section. | The power take-off system is a crucial part of wave energy converters, which largely determines the cost, efficiency and reliability of the WEC. Many studies focus on optimisation of the PTOs; several challenges related to PTOs are mentioned in the previous section. | ||
Line 119: | Line 133: | ||
==External links== | ==External links== | ||
− | [https://www.ocean-energy-systems.org/documents/84169-oes-spotlight-on-ocean-energy.pdf/ Ocean Energy Systems website, 2018 report Spotlight on ocean energy] | + | :[https://www.ocean-energy-systems.org/documents/84169-oes-spotlight-on-ocean-energy.pdf/ Ocean Energy Systems website, 2018 report Spotlight on ocean energy] |
− | + | :[https://en.wikipedia.org/wiki/List_of_wave_power_projects List of wave power projects] | |
==Further reading== | ==Further reading== | ||
Line 130: | Line 144: | ||
− | ==Appendix: Wave energy flux at the European Atlantic coast== | + | ==Appendix A: Wave energy flux at the European Atlantic coast== |
For regular water waves, the time-mean [[waves|wave]] energy density <math>E</math> per unit horizontal area on the water surface [J/m<sup>2</sup>] is the sum of kinetic and potential energy density per unit horizontal area. The potential energy density is equal to the kinetic energy <ref name="ref1">Mei C.C. 1989. The applied dynamics of ocean surface waves. Advanced series on ocean engineering. World Scientific Publishing Ltd </ref> both contributing half to the time-mean wave energy density <math>E</math> that is proportional to the wave height squared according to linear wave theory <ref name="ref1"/> (see [[Shallow-water wave theory]]): | For regular water waves, the time-mean [[waves|wave]] energy density <math>E</math> per unit horizontal area on the water surface [J/m<sup>2</sup>] is the sum of kinetic and potential energy density per unit horizontal area. The potential energy density is equal to the kinetic energy <ref name="ref1">Mei C.C. 1989. The applied dynamics of ocean surface waves. Advanced series on ocean engineering. World Scientific Publishing Ltd </ref> both contributing half to the time-mean wave energy density <math>E</math> that is proportional to the wave height squared according to linear wave theory <ref name="ref1"/> (see [[Shallow-water wave theory]]): | ||
Line 153: | Line 167: | ||
[[File:Time-mean wave energy flux along West European coasts.jpg|thumb|280px|right| | [[File:Time-mean wave energy flux along West European coasts.jpg|thumb|280px|right| | ||
− | Fig | + | Fig 12: Time-mean wave energy flux along <br> West European coasts<ref name = ref3>Mattarolo, G., Benoit, M. and Lafon, F. 2009. Wave energy resource off the French coasts: the ANEMOC database applied to the energy yield evaluation of Wave Energy, 10th European Wave and Tidal Energy Conference Series (EWTEC’2009), Uppsala (Sweden)</ref>.]] |
Equation (5) can be reduced to (4) with the hypothesis of regular waves in deep water. The directional spectrum is deduced from directional wave buoys, SAR images or advanced spectral wind-wave models, known as third-generation models, such as WAM, WAVEWATCH III, TOMAWAC or SWAN. These models solve the spectral action balance equation without any a priori restrictions on the spectrum for the evolution of wave growth. | Equation (5) can be reduced to (4) with the hypothesis of regular waves in deep water. The directional spectrum is deduced from directional wave buoys, SAR images or advanced spectral wind-wave models, known as third-generation models, such as WAM, WAVEWATCH III, TOMAWAC or SWAN. These models solve the spectral action balance equation without any a priori restrictions on the spectrum for the evolution of wave growth. | ||
− | The nearshore wave atlas ANEMOC along the Atlantic coast of Europe is based on numerical simulation with the TOMAWAC model of the wave climate over 25 years<ref name="Ref 2">Benoit, M. and Lafon. F. 2004. A nearshore wave atlas along the coasts of France based on numerical modelling of the wave climate over 25 years, 29th International Conference on Coastal Engineering (ICCE’2004), Lisbonne (Portugal), pp 714-726</ref>. Using equation (5), the time-mean wave energy flux along West European coasts is obtained, shown in Fig. | + | The nearshore wave atlas ANEMOC along the Atlantic coast of Europe is based on numerical simulation with the TOMAWAC model of the wave climate over 25 years<ref name="Ref 2">Benoit, M. and Lafon. F. 2004. A nearshore wave atlas along the coasts of France based on numerical modelling of the wave climate over 25 years, 29th International Conference on Coastal Engineering (ICCE’2004), Lisbonne (Portugal), pp 714-726</ref>. Using equation (5), the time-mean wave energy flux along West European coasts is obtained, shown in Fig. 12. This equation still presents some limits like the definition of the bounds of the integration. Moreover, getting data on the wave energy near coastal structures requires the use of numerical models that are able to represent the physical processes of wave transformation in shallow or intermediate water due to refraction, shoaling, dissipation by bottom friction or by wave breaking, interactions with tides and diffraction by islands. |
The wave energy flux is therefore usually calculated for water depths superior to 20 m. This maximal energetic resource calculated in deep water will be limited in the coastal zone: | The wave energy flux is therefore usually calculated for water depths superior to 20 m. This maximal energetic resource calculated in deep water will be limited in the coastal zone: | ||
Line 163: | Line 177: | ||
:* at high tide during storm events, when the wave height exceeds the maximal operating conditions; | :* at high tide during storm events, when the wave height exceeds the maximal operating conditions; | ||
:* by screen effects due to the presence of capes, spits, reefs, islands,... | :* by screen effects due to the presence of capes, spits, reefs, islands,... | ||
+ | The total European wave energy resource is estimated in the range 1000-1500 TWh/yr<ref>EC 2017. Study on Lessons for Ocean Energy Development. Directorate-General for Research and Innovation. Publications Office of the European Union. EUR 27984 EN</ref>. | ||
+ | |||
+ | ==Appendix B== | ||
+ | Buoys that generate energy by going up and down with the wave motion, the so-called point absorbers, are the most common wave energy conversion systems in deep water (see section point absorbers). The energy yield is greatest when the buoy's resonance frequency is equal to the wave frequency. A theoretical model, which only applies to small monochromatic waves, shows that the maximum power <math>P_{max}</math> [W] that a point absorber can generate in such a wave field is given by the product of the average wave energy flux per unit crest length <math>P_w</math> [W/m ] divided by the wavenumber <math>k=2 \pi / \lambda </math> [1/m]<ref>Evans, D.V. 1976. A theory for wave-power absorption by oscillating bodies. J. Fluid Mech. 77: 1–25</ref>. This means that the size of the point absorber does not really matter. Unfortunately, the practice is less favorable, on the one hand because the strong variability that is characteristic for sea conditions makes that resonance only occurs in exceptional cases, and on the other hand because the greatest energy output does not correspond to small wave amplitudes. The capture width ratio <math>\eta</math> of wave energy converters is defined as | ||
+ | |||
+ | <math>\eta = \Large\frac{P}{B P_w}\normalsize , \qquad (B1)</math> | ||
+ | |||
+ | where <math>P</math> is the average energy absorbed by the device and <math>B</math> a representative width of the device (or length in the case of attenuators). | ||
+ | The capture width ratios achieved by prototype models of the different types of wave energy converters are in the following ranges<ref>Babarit A. and Hals J. 2011. On the maximum and actual capture width ratio of wave energy converters – 11th European Wave and Tidal Energy Conference Series (EWTEC’2011) – Southampton (U-K)</ref>: | ||
+ | * Oscillating water column devices 15-40% (typical width <math>B \sim</math> 30 m) | ||
+ | * Overtopping devices 4-23% (typical width/length <math>B \sim</math> 300 m) | ||
+ | * Point absorbers 3-42% (typical width/length <math>B \sim </math> 5-20 m; the lower percentages are for the smaller devices) | ||
+ | * Terminators 41-65% (typical width/length <math>B \sim </math> 20 m) | ||
+ | * Floating pitching devices 20-36% (typical width/length <math>B \sim</math> 25 m) | ||
+ | * Attenuators 5-7% (typical length <math>B \sim </math> 150 m) | ||
+ | |||
Revision as of 12:16, 13 January 2021
Contents
- 1 Introduction
- 2 Wave Energy Conversion Principles
- 3 Power take-off systems (PTO)
- 4 Issues with wave energy converters
- 5 Wave energy converters combined with offshore wind
- 6 International organizations
- 7 Related articles
- 8 External links
- 9 Further reading
- 10 Appendix A: Wave energy flux at the European Atlantic coast
- 11 Appendix B
- 12 References
Introduction
Vast and reliable, wave power has long been considered as one of the most promising renewable energy sources. In a special IPCC 2011 report[1] several estimates are presented for the world total potential of ocean wave energy resources. These estimates were obtained using methods as illustrated in Appendix A. The theoretical maximum has been estimated at about 30,000 TWh/yr (3.1013 kWh/yr), which is about 20% of the 2019 world energy consumption. However, given technological and economic constraints, the exploitable resource is probably almost a factor 10 less.
Wave Energy Converters (WECs) convert wave power into electricity. Although attempts to utilize this resource date back to at least 1890, wave power is currently not widely employed[2]. The operational wave power installed worldwide in 2020 totaled approximately 16 MW [2], which is about 5 orders of magnitude less than the 2-3 TW required to exploit the global wave energy potential. An important reason is the production costs per kWh, which were in 2020 about a factor 10 higher compared to offshore wind farms [3].
A plethora of innovational methods for wave power conversion have been invented in the last three decades, resulting in thousands of patents over recent years. At present, a number of different wave energy concepts are being investigated by companies and academic research groups around the world. Although many working designs have been developed and tested through modelling and wave tank-tests, only a few concepts have progressed to sea testing. Strong cost reductions, which are only possible with a sharp increase in global application, should enable wave plants to compete favorably with conventional power plants in the future[4].
Wave Energy Conversion Principles
In this section the most popular current methods for wave energy conversion are briefly presented. An indication of the efficiency of these methods is presented in Appendix B.
Oscillating Water Columns
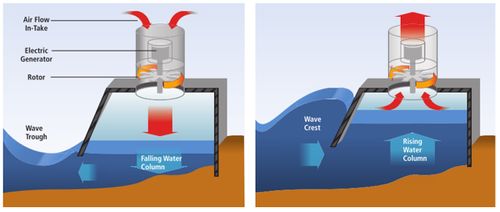
The principle of the oscillating water column is illustrated in Fig. 1, in this example for use in conjunction with a fixed structure (e.g., breakwater). The functioning of the oscillating water columns (OWCs) is somewhat similar to that of a wind turbine, being based on the principle of wave induced air pressurization. The device is set upon a closed air chamber, which is placed above the water. The passage of waves changes the water level within the closed housing and the rising and falling water level increases and decreases the air pressure within the housing introducing a bidirectional air flow. By placing a turbine on top of this chamber air will pass in and out of it with the changing air pressure levels.
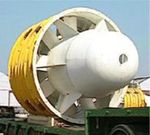
There are two options to separate the bi-directional flow: a Wells turbine to create suction or alternatively, pressure generating valves[6]. The Wells turbine is constructed such that it rotates always in the same direction regardless of airflow direction, see Fig. 2. The efficiency is lower (50-60%) than with conventional turbines, but higher than achievable with conventional turbines in alternating mode[7].
OWC devices can be moored offshore but they can also be placed near the shore where waves break. This results in significant cost savings. The disadvantage is the shallow water depth along the shore, which dampens the largest waves. See also Wave energy converters in coastal structures.
Special buoys have been developed for the application of OWC converters in deep water, according to the principle of Fig. 3. The length of the shaft determines the resonance frequency, allowing optimum energy efficiency to be achieved. An example of an offshore OWC is the Spar Buoy, Fig. 4. The original concept was invented by Yoshio Masuda (1925-2009), who developed navigation buoys powered by wave energy, equipped with an air turbine. It is circular in plane and therefore invariant to wave direction (Fig. 4). The size varies according to the target sea conditions at the deployment site but maximum dimensions were estimated at 30 m diameter, 50 m height and 35 m draft, which could deliver up to 450 kW.
Overtopping Devices
Another type of wave energy converter is the overtopping device, which operates somewhat similar to a hydroelectric dam. The "Wave Dragon" created by Wave Dragon ApS[8] is the best known example of an offshore overtopping device (Fig. 5). Its floating arms focus waves onto a slope from which the wave overtops into a reservoir. The resulting difference in water elevation between the reservoir and the mean sea level then drives low-head hydro turbines. It was estimated that an optimal size design of 260 m width and 150 m length can produce up to 4 MW. In wave climates above 33 kW/m, this technology was expected to be economically competitive with offshore wind power in the near future. After a combined cost saving and power efficiency increase, the power price could eventually be in line with costs of fossil fuel generation[9]. However, a feasibility study for a Wave Dragon deployment at the northern Spanish coast published in 2020 reported costs which were still a factor 10 higher[10].
Near the shore, overtopping converters can be installed in front of or as part of caisson breakwaters. An example is the SeaWave Slot-Cone Generator (SSG)[11], which collects seawater by wave overtopping over several reservoirs placed above each other, resulting in high hydraulic efficiency, see Wave energy converters in coastal structures.
Wave absorbing devices
A great number of different devices have been developed to harness wave energy directly by using wave-induced water motion. The most popular types are displayed schematically in Fig. 6.
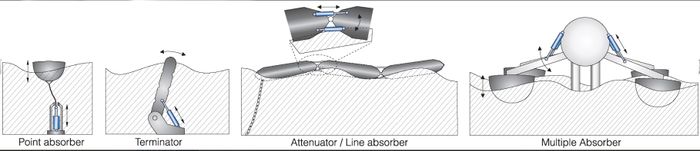
Point absorbers
Point absorber are buoy-type wave energy converters (WECs) that harvest incoming wave-energy from all directions. They are placed offshore at the ocean surface or just below. A vertically submerged floater absorbs wave energy which is converted by a piston or linear generator into electricity. One such a point absorber WEC is the FO3 concept developed by Norwegian entrepreneur Fred Olsen. It consists of several (12 or 21) heaving floaters attached to a 36 by 36 meter rig (Fig. 7 top). By means of a hydraulic system, the vertical motion is converted into a rotational movement that drives the hydraulic motor. This motor in turn powers the generator that can produce up to 2,52 MW[13].
The multiple point absorber type WEC "Wave Star", developed by Wave Star ApS[14], has a number of floaters on movable arms (Fig. 7 bottom). The energy of the motion of the arms is again captured in a common hydraulic line and converted into electric current. Most noticeably, being able to raise the entire installation along its pillars, this system has a high endurance for rough storm conditions. So far, this method has not been deployed at full scale. A 1:2 scaled installation has been built at Hanstholm which turns out 600 kW. However, production is thought to be scale-able up to 6 MW[15]. A major benefit of these types of exploitation is the minimal contact with water, placing any delicate machinery and electrics out of reach of any corrosion or physical forcing of the waves. The Wave Star development was abandoned in 2016.
Terminators
Terminators consist of flaps that rotate with the wave orbital motion around an axis parallel to the wave front. Examples are the Oyster (Fig. 8a) and the WaveRoller(Fig. 8b), both bottom-hinged terminators and the Salter Duck (Fig. 8c), with a rotation axis near the surface. Although these designs capture wave energy with a high efficiency (see Appendix B), no large-scale operational deployments have been realized. They are installed in intermediate depths, not far from the shore, where the wave front direction is most of the time close to shore-parallel. Oyster and WaveRoller have been tested in nature; for Salter Duck no full-scale prototype was built. Oyster’s electrical output is generated by an hydro-electric turbine onshore, driven by high pressure water via subsea pipelines. WaveRoller is equipped with an on board hydraulic system that drives an electricity generator, which is connected to the electric grid via a subsea cable. Hinged wave surge converters generally use hydraulic systems for power take-off. Hydraulic systems are well suited to harvest energy from high-force, slow-oscillatory motions which have to be converted to rotary motion and drive a generator. In order to rectify the fluctuating wave power, which would result in variable electrical power output unsuited to the electrical grid, some sort of energy storage system (or other means of compensation, such as an array of devices) is usually incorporated in the PTO system, such as accumulators, which can function as short term energy storage, helping the system handle the fluctuations[7].
Wave attenuators
The "DEXA", developed and patented by DEXA Wave Energy ApS [16], is an illustrative example of a wave attenuator. The device consists of two hinged catamarans that pivot relative to the other (Fig. 9). The resulting oscillatory flux at the hinge, is harnessed by means of a water-based low pressure power transmission that restrains angular oscillations. Flux generation is optimized by placing the floaters of each catamaran half a wavelength apart. A scaled prototype (dimensions 44x16.2m[17]) placed in the Danish part of the North Sea should generate 160 kW[18]. Full-scale models are thought to be able to generate up to 250 kW[16]. However, the DEXA development was terminated in 2012.
Power take-off systems (PTO)
The power take-off (PTO) system of a wave energy converter has a direct impact on the capital cost of a project by usually accounting for between 20 and 30% of the overall investment. The economic viability, efficiency and complexity of a wave energy converter depends largely on its PTO system. Maintenance at sea is a demanding and expensive task; high reliability and durability of all components of the PTO system are therefore required. This is technically challenging for systems exposed to the harsh marine environment, especially systems that consist of many moving parts that are exposed to corrosion and fouling. Several popular PTO systems have been reviewed by Ahamed et al. (2020[19]), from which the summary below is extracted.

Oscillating water column wave converters (OWC) generally use the previously described Wells turbine as PTO system. These turbines are vulnerable due to the relatively large number of moving parts. Overtopping devices are generally equipped with hydro turbines for power take-off. Conventional hydro turbines require for high efficiency more head and flow than provided by overtopping ocean waves. Wave absorbing devices use hydraulic motor systems or direct mechanical or electrical drive PTO systems. Hydraulic motor-based PTO systems are suited for converting the low-speed oscillating motion into energy. However, the hydraulic motor-based PTO system consists of many mechanical moving parts and due to compression and decompression of the fluid there is a risk of hydraulic oil leakage. Direct mechanical drive uses linear-to-rotary conversion systems without pneumatic or hydraulic systems. The efficiency is high, but the lifetime is relatively short and maintenance costs are substantial. Direct electrical drive transmits the wave energy into electrical energy directly by coupling the mechanical energy to the moving part of a linear generator (Fig. 10). Issues are the need for a heavy structure due to the attractive forces between the stator and the translator and the complicated power transmission system due to the unequal generated voltage created by the irregular wave motion.
The 'Triboelectric nanogenerator' (TENG) and its extension, the 'Triboelectric−Electromagnetic Hybrid Nanogenerator' (TENG-EMG)[20], are a new development that can efficiently harvest energy in any frequency range, are low-cost lightweight, easy to fabricate and easy to be scaled (size of individual units being below the micrometer scale). The nanogenerator uses a polymer-metal pair to create contact electrification (triboelectric effect) between two materials sliding against each other and to induce charge transfer between their electrodes due to electrostatic induction, either in a layer structure or in a spherical-shell structure[21], see Fig. 11. Challenges for application in a prototype lie in the use of TENGs for power transfer to the shore, cost to scale, lifetime of the TENG materials in the ocean environment and connection methods of the thousands of TENG units that are needed.

Issues with wave energy converters
To be able to produce energy at competitive prices, several obstacles have to be overcome. The following factors in particular determine the high costs of wind energy.
A very robust construction made of high quality materials is required that remains intact under severe storms and withstands the demanding conditions at sea, leading to corrosion, fouling and fatigue. The classical protection measure against fouling and corrosion of steel structures is regular maintenance and repainting. But this is time-consuming and costly because of the difficult access to offshore installations, especially under harsh conditions when damage occurs. In addition, the use of antifouling paints may be detrimental to the marine environment (e.g. Tributyltin paints[22]). Full-scale devices out of concrete may provide a valuable alternative since concrete is long-lived if properly mixed[23]. The cost of repairs is a major component of the wave farm costs. The reliability of the components, especially due to the cost of eventual repair actions, is pivotal for the economic viability of a project[24]. Deployments should be capable of lasting 30 years or more. This is a tall order as demonstrated by the mooring of the Wave Dragon that failed during a severe storm on the 8th of january 2004.
The power generated by ocean waves fluctuates strongly due to the irregular wave climate, which makes connection to the electricity grid difficult[25]. In addition, connection points to the electricity grid may not be available in areas where the conditions for wave energy generation are most favorable.
Crucial for any design is the mooring which ensures a maintained position under both normal operating loads as well as extreme storm load conditions. It should not exert excess tension loads on the electrical transmission cables and ensure the suitable safety distances between devices in multiple installations. Most commonly, a free hanging catenary configuration is used for mooring but multi-catenary systems and flexible risers are not infrequent as well. Every configuration should be sufficiently compliant to accommodate tidal variations and environmental loading while remaining sufficiently stiff to allow berthing for inspections and maintenance.
Due to the great variability of the wave climate with rare extremes, it is important to be able to test prototype designs over a long period before they are deployed on a large scale. Mathematical simulation models can be of great value here, because this is a quick and relatively inexpensive way to test a design for its effectiveness and efficiency at the long term, both in terms of capital and operational expenses, in order to achieve the lowest overall cost of electricity. For this purpose, the modeling tool supports the decision-maker in the pursuit of the most reliable and easy to maintain device design but also reports the trade-off between energetic yield and operational and maintenance efforts[24].
The power take-off system is a crucial part of wave energy converters, which largely determines the cost, efficiency and reliability of the WEC. Many studies focus on optimisation of the PTOs; several challenges related to PTOs are mentioned in the previous section.
Wave energy converters combined with offshore wind
The high cost of stand-alone wave energy conversion schemes is a major obstacle for its large-scale application. However, costs can be significantly reduced by combining WECs with structures offshore or along the coast that are being built for other applications. A good example is the integration of WECs with breakwaters in the coastal zone. This is described in the article Wave energy converters in coastal structures.
Another possible combination is the integration of wind and wave energy production. This is especially interesting in areas where the conditions for optimal wind energy production do not systematically coincide with conditions for optimal wave energy production. It is also a way to make optimal use of marine space[26]. The main advantage of integrated wind power generation is shared infrastructure costs, especially foundations and grid connections. However, with the existing WEC techniques, the costs per kWh produced are still higher with a combined wind-wave application than with wind energy alone[27]. Synergy benefits can also be sought through improved stability of the structure, for example in the case of an OWC wave energy converter integrated into an offshore wind turbine monopile[28]. Stability improvement can be a major benefit for designs in which the interaction between the wind and wave sub-structures is strong, as in the case of a WEC combined with a floating wind turbine[29]. Wave energy converters can also reduce wave heights inside a wind farm, increasing in this way the weather windows to access the wind turbines[30].
International organizations
Several organizations have been established for worldwide collaboration on ocean wave energy development involving research institutes, wave energy developers, operators and governments.
Ocean Energy Europe (OEE), a not-for-profit organization, is a network of ocean energy professionals collaborating with 120 organizations, including Europe’s top utilities, industrialists and research institutes. It aims to create a strong environment for the development of ocean energy, improve access to funding, and enhance business opportunities for its members. To this end, OEE engages with the European Institutions (Commission, Parliament, Council, EIB, etc.), and national ministries on policy issues affecting the sector. Ocean Energy Europe also organizes the annual Ocean Energy Europe Conference and Exhibition – the annual event which gathers representatives from the industry, Ministers and Commissioners.
The Ocean Energy Systems Technology Collaboration Programme (OES), established by the International Energy Agency (IEA), is an international organisation that is actively collaborating between its 29 member countries with the aim of advancing ocean energy research, development and demonstration of technologies to generate electricity from ocean energy resources (Wave, Tidal Range, Tidal and Ocean Currents, Ocean Thermal Energy Conversion (OTEC) and Salinity Gradients). The primary education and research initiatives of OES are aimed at promoting the feasibility, recognition and adoption of ocean energy systems in an environmentally acceptable manner.
The European Marine Energy Centre (EMEC) Ltd provides developer companies, wave and tidal energy converter-technology developer with certified open-sea testing services. The objective of EMEC is to decrease the time, cost, and risk related with marine energy technology development, increasing the use of EMEC’s modified facilities as well as industry knowledge and other experiences. EMEC has 13 grid connected test berths where many marine energy converters have been installed. EMEC is an independent organization that maintains relations with various developer companies, academic organizations and governing bodies and presently working with companies and researchers to broaden research programmes to solve a variety of environmental and operational challenges relevant to industry.
The European Network for marine renewable energy (WECANet) is a network of 31 partner countries to assist networking, training and collaboration in Europe. Four working groups address the following topics: numerical modelling for WECs, experimental hydrodynamic modelling including PTO systems, technology development and economical / political aspects.
OCEANERA-NET organizes funding programmes to support research and innovation between European countries and regions in the ocean energy sector.
International conferences on ocean energy are organized by
- European Wave and Tidal Energy Conference (EWTEC). Selected peer-reviewed conference contributions are published in the EWTEC’s International Marine Energy Journal.
- Asian Wave and Tidal Energy conference (AWTEC) addresses updates on recent global activities and initiatives with a distinctly special interest in the Asian region. The conference cooperates with the Journal of Marine Science and Engineering for publication of selected conference contributions.
- International Conference on Ocean Energy (ICOE) is a biennial global marine energy event focused on the industrial development of renewable marine energy. ICOE is a collaboration with the IEA Technology Collaboration Programme – Ocean Energy Systems (OES).
Related articles
External links
Further reading
- Drew, B., Plummer, A.R.and Sahinkaya, M.N. 2009. A review of wave energy converter technology. Proceedings of the Institution of Mechanical Engineers, Part A: Journal of Power and Energy 223(8): 887-902 [3]
For an overview of the current status (2018) and recent technological developments (2020) regarding Wave Energy Converters, the reader is referred to the publications:
- Ahamed, R., McKee, K. and Howard, I. 2020. Advancements of wave energy converters based on power take off (PTO) systems: A review. Ocean Engineering 204, 107248
- Aderinto, T. and Li, H. 2018. Ocean Wave Energy Converters: Status and Challenges. Energies 11, 1250; doi:10.3390/en11051250 (open access)
Appendix A: Wave energy flux at the European Atlantic coast
For regular water waves, the time-mean wave energy density [math]E[/math] per unit horizontal area on the water surface [J/m2] is the sum of kinetic and potential energy density per unit horizontal area. The potential energy density is equal to the kinetic energy [31] both contributing half to the time-mean wave energy density [math]E[/math] that is proportional to the wave height squared according to linear wave theory [31] (see Shallow-water wave theory):
[math]E= \large\frac{1}{8}\normalsize \rho g H^2 , \qquad (1)[/math]
where [math]g[/math] is the gravity acceleration and [math]H[/math] the wave height of regular water waves. As the waves propagate, their energy is transported. The energy transport velocity is the group velocity. As a result, the time-mean wave energy flux per unit crest length [W/m] perpendicular to the wave propagation direction, is equal to [31]:
[math] P = E \times c_{g} , \qquad (2)[/math]
with [math]c_{g}[/math] the group velocity [m/s]. Due to the dispersion relation for water waves under the action of gravity, the group velocity depends on the wavelength [math]\lambda[/math] [m], or equivalently, on the wave period [math]T [/math][s]. Further, the dispersion relation is a function of the water depth [math]h[/math] [m]. As a result, the group velocity behaves differently in the limits of deep water ([math]h \gt \lambda / 2[/math]), shallow water ([math]h \lt \lambda/20[/math]), and at intermediate depths ([math]\lambda /20 \lt h \lt \lambda / 2[/math]). For regular waves in deep water
[math]c_{g} = \large\frac{gT}{4\pi}\normalsize [/math] and [math]P_{w1} = \large\frac{\rho g^2}{32 \pi}\normalsize H^2 T . \qquad (3)[/math]
The time-mean wave energy flux per unit crest length is used as one of the main criteria to choose a site for wave energy converters. For real seas, whose waves are random in height, period and direction, the spectral parameters have to be used (for the definition of spectral wave parameters, see the article Statistical description of wave parameters). The spectral estimate of significant wave height [math]H_{m0}[/math] is calculated from the zero-order moment of the spectral function [math]m_0[/math] according to [math]H_{m0} = 4 \sqrt{m_0} [/math]. The relevant wave period is the mean energy period [math]T_E \equiv T_{m-1,0}[/math] [32],
[math]P_{w1} = \large\frac{\rho g^2}{64 \pi}\normalsize H_{m0}^2 T_E . \qquad (4)[/math]
If local data are available for a sea state ([math]H_{m0}^2, T_E [/math]) through in-situ wave buoys, satellite data or numerical modelling, Eq. (4) provides a first estimate of the wave energy flux. Averaged over a season or a year, it represents the maximal energetic resource that can be theoretically extracted from wave energy. If the directional spectrum of sea state variance [math]E(f,\theta)[/math] is known with [math]f[/math] the wave frequency [Hz] and [math]\theta[/math] the wave direction [rad], a more accurate formulation is used:
[math]P_{w2} = \rho g\int\int c_{g}(f,h)E(f,\theta) dfd \theta . \qquad (5)[/math]
Equation (5) can be reduced to (4) with the hypothesis of regular waves in deep water. The directional spectrum is deduced from directional wave buoys, SAR images or advanced spectral wind-wave models, known as third-generation models, such as WAM, WAVEWATCH III, TOMAWAC or SWAN. These models solve the spectral action balance equation without any a priori restrictions on the spectrum for the evolution of wave growth.
The nearshore wave atlas ANEMOC along the Atlantic coast of Europe is based on numerical simulation with the TOMAWAC model of the wave climate over 25 years[34]. Using equation (5), the time-mean wave energy flux along West European coasts is obtained, shown in Fig. 12. This equation still presents some limits like the definition of the bounds of the integration. Moreover, getting data on the wave energy near coastal structures requires the use of numerical models that are able to represent the physical processes of wave transformation in shallow or intermediate water due to refraction, shoaling, dissipation by bottom friction or by wave breaking, interactions with tides and diffraction by islands.
The wave energy flux is therefore usually calculated for water depths superior to 20 m. This maximal energetic resource calculated in deep water will be limited in the coastal zone:
- at low tide, by wave breaking;
- at high tide during storm events, when the wave height exceeds the maximal operating conditions;
- by screen effects due to the presence of capes, spits, reefs, islands,...
The total European wave energy resource is estimated in the range 1000-1500 TWh/yr[35].
Appendix B
Buoys that generate energy by going up and down with the wave motion, the so-called point absorbers, are the most common wave energy conversion systems in deep water (see section point absorbers). The energy yield is greatest when the buoy's resonance frequency is equal to the wave frequency. A theoretical model, which only applies to small monochromatic waves, shows that the maximum power [math]P_{max}[/math] [W] that a point absorber can generate in such a wave field is given by the product of the average wave energy flux per unit crest length [math]P_w[/math] [W/m ] divided by the wavenumber [math]k=2 \pi / \lambda [/math] [1/m][36]. This means that the size of the point absorber does not really matter. Unfortunately, the practice is less favorable, on the one hand because the strong variability that is characteristic for sea conditions makes that resonance only occurs in exceptional cases, and on the other hand because the greatest energy output does not correspond to small wave amplitudes. The capture width ratio [math]\eta[/math] of wave energy converters is defined as
[math]\eta = \Large\frac{P}{B P_w}\normalsize , \qquad (B1)[/math]
where [math]P[/math] is the average energy absorbed by the device and [math]B[/math] a representative width of the device (or length in the case of attenuators). The capture width ratios achieved by prototype models of the different types of wave energy converters are in the following ranges[37]:
- Oscillating water column devices 15-40% (typical width [math]B \sim[/math] 30 m)
- Overtopping devices 4-23% (typical width/length [math]B \sim[/math] 300 m)
- Point absorbers 3-42% (typical width/length [math]B \sim [/math] 5-20 m; the lower percentages are for the smaller devices)
- Terminators 41-65% (typical width/length [math]B \sim [/math] 20 m)
- Floating pitching devices 20-36% (typical width/length [math]B \sim[/math] 25 m)
- Attenuators 5-7% (typical length [math]B \sim [/math] 150 m)
References
- ↑ 1.0 1.1 Lewis, A., Estefen, S., Huckerby, J., Musial, W., Pontes, T. and Torres-Martinez, J. 2011. Ocean Energy. In IPCC Special Report on Renewable Energy Sources and Climate Change Mitigation [O. Edenhofer, R. Pichs-Madruga, Y. Sokona, K. Seyboth, P. Matschoss, S. Kadner, T. Zwickel, P. Eickemeier, G. Hansen, S. Schlömer, C. von Stechow (eds)], Cambridge University Press, Cambridge, United Kingdom and New York, NY, USA.
- ↑ Miller, C. 2004. A Brief History of Wave and Tidal Energy Experiments in San Francisco and Santa Cruz. [1]
- ↑ IRENA, 2014. Ocean Energy Technology Brief 4, www.irena.org
- ↑ Pelc, R. and Fujita, R.M. 2002. Renewable energy from the ocean. Marine Policy, 26: 471-479.
- ↑ Falcao, F.O. and Henriques, J.C.C. 2016. Oscillating-water-column wave energy converters and air turbines: A review. Renewable Energy 85: 1391-1424
- ↑ Kofoed, J.P. and Frigaard, P., 2008. Hydraulic evaluation of the LEANCON wave energy converter. DCE Technical Report No. 45. Dep. of Civil Eng., Aalborg University, Oct. 2008. Leancon Wave Energy. Leancon website
- ↑ 7.0 7.1 Drew, B., Plummer, A.R. and Sahinkaya, M.N. 2009. A review of wave energy converter technology. Proceedings of the Institution of Mechanical Engineers, Part A: Journal of Power and Energy 223(8): 887-902
- ↑ Wave Dragon ApS Wave Dragon website
- ↑ Christensen, L., Friis-Madsen, E., Kofoed, J.P., 2005. The Wave Energy Challenge: The Wave Dragon case. PowerGen 2005 Europe Conference - Wave Dragon, 20pp.
- ↑ Castro-Santos, L., Bento, A.R. and Soares, C.G. 2020. The Economic Feasibility of Floating Offshore Wave Energy Farms in the North of Spain. Energies 13, 806; doi:10.3390/en13040806
- ↑ Vicinanza, D., Margheritini, L., Kofoed, J.P. and Buccino, M. 2012.The SSG Wave Energy Converter: Performance, Status and Recent Developments. Energies 5: 193-226
- ↑ Hansen, R.H., Kramer, M.M. and Vidal, E. 2013. Discrete Displacement Hydraulic Power Take-Off System for the Wavestar Wave Energy Converter. Energies 6: 4001-4044; doi:10.3390/en6084001
- ↑ Leirbukt, A. and Tubaas, P. 2006. A wave of renewable energy. ABB Review 3: 29-31
- ↑ Wave Star ApS website
- ↑ Bjerrum, A. 2008. Wave Energy - new unlimited source of energy. European Renewable Energy Conference presentation.
- ↑ 16.0 16.1 Dexawave Energy ApS. Dexawave website
- ↑ Kofoed, J.P. 2009. Hydraulic evaluation of the DEXA wave energy converter. DCE Technical Report No. 57. Dep. of Civil Eng., Aalborg University, 23 pp.
- ↑ Martinelli L., Zanuttigh,B. and Kofoed, J.P. 2009. Statistical analysis of power production from OWC type wave energy converters. EWTEC Conference, Uppsala, 7-11 Sept 2009
- ↑ 19.0 19.1 Ahamed, R., McKee, K. and Howard, I. 2020. Advancements of wave energy converters based on power take off (PTO) systems: A review. Ocean Engineering 204, 107248
- ↑ Wen, Z., Guo, H., Zi, Y., Yeh, M.-H., Wang, X., Deng, J., Wang, J., Li, S., Hu, C. and Zhu, L. 2016. Harvesting broad frequency band blue energy by a triboelectric–electromagnetic hybrid nanogenerator. ACS Nano 10 (7): 6526–6534
- ↑ 21.0 21.1 Huang, B., Wang, P., Wang, L., Yang, S. and Wu, D. 2020. Recent advances in ocean wave energy harvesting by triboelectric nanogenerator: An overview Nanotechnology Reviews 9(1)
- ↑ Paul, J.D. and Davies, I.M. 1986. Effects of copper- and tin-based anti-fouling compounds on the growth of scallops (Pecten maximus) and oysters (Crassostrea gigas). Aquaculture 54: 191-203
- ↑ Metha, P.K. 2001. Reducing the Environmental Impact of Concrete. Concrete International October 61-66
- ↑ 24.0 24.1 Rinaldi, G., Portillo, J.C.C., Khalid, F., Henriques, J.C.C., Thies, P.R., Gato, L.M.C. and Johanning, L. 2018. Multivariate analysis of the reliability, availability, and maintainability characterizations of a Spar–Buoy wave energy converter farm. Journal of Ocean Engineering and Marine Energy 4: 199–215
- ↑ Sjolte, J. 2014. Marine Renewable Energy Conversion: Grid and Off-Grid Modeling, Design and Operation. Doctoral Thesis, Norges Teknisk-Naturvitenskapelige Universitet, Trondheim, Norway
- ↑ Azzellino, A., Lanfredi, C., Riefolo, L., De Santis, V., Contestabile, P. and Vicinanza, D. 2019. Combined exploitation of offshore wind and wave energy in the Italian seas: a spatial planning approach. Frontiers in Energy Research 7, 42
- ↑ Clark, C., Miller, A. and DuPont, B. 2017. Analytical Cost Modeling for Co-Located Wind-Wave Energy Arrays. Proceedings of the 12th European Wave and Tidal Energy, Cork, Ireland, paper 871
- ↑ Zhou, Y., Ning, D., Shi, W., Joanning, L. and Liang, D. 2020. Hydrodynamic investigation on an OWC wave energy converter integrated into an offshore wind turbine monopile. Coastal Engineering 162, 103731
- ↑ Zhu, H., Hu, C., Sueyoshi, M. and Yoshida, S. 2020. Integration of a semisubmersible floating wind turbine and wave energy converters: an experimental study on motion reduction. J. Mar. Sci. Technol. 25: 667–674
- ↑ Perez-Collazo, C., Greaves, G. and Iglesias, G. 2015. A review of combined wave and offshore wind energy. Renewable and Sustainable Energy Reviews 42: 141-153
- ↑ 31.0 31.1 31.2 Mei C.C. 1989. The applied dynamics of ocean surface waves. Advanced series on ocean engineering. World Scientific Publishing Ltd
- ↑ Vicinanza D., Cappietti L., Ferrante V. and Contestabile P. 2011. Estimation of the wave energy along the Italian offshore, Journal of Coastal Research 64: 613 - 617
- ↑ Mattarolo, G., Benoit, M. and Lafon, F. 2009. Wave energy resource off the French coasts: the ANEMOC database applied to the energy yield evaluation of Wave Energy, 10th European Wave and Tidal Energy Conference Series (EWTEC’2009), Uppsala (Sweden)
- ↑ Benoit, M. and Lafon. F. 2004. A nearshore wave atlas along the coasts of France based on numerical modelling of the wave climate over 25 years, 29th International Conference on Coastal Engineering (ICCE’2004), Lisbonne (Portugal), pp 714-726
- ↑ EC 2017. Study on Lessons for Ocean Energy Development. Directorate-General for Research and Innovation. Publications Office of the European Union. EUR 27984 EN
- ↑ Evans, D.V. 1976. A theory for wave-power absorption by oscillating bodies. J. Fluid Mech. 77: 1–25
- ↑ Babarit A. and Hals J. 2011. On the maximum and actual capture width ratio of wave energy converters – 11th European Wave and Tidal Energy Conference Series (EWTEC’2011) – Southampton (U-K)
Please note that others may also have edited the contents of this article.
|
Please note that others may also have edited the contents of this article.
|