Difference between revisions of "Sand-filled geosystems in coastal engineering"
Dronkers J (talk | contribs) |
Dronkers J (talk | contribs) |
||
(One intermediate revision by the same user not shown) | |||
Line 165: | Line 165: | ||
Several research results suggest that the hydraulic stability of sand-filled geosystems can be checked by means of the following equation: | Several research results suggest that the hydraulic stability of sand-filled geosystems can be checked by means of the following equation: | ||
− | <math>\frac{H_S}{\Delta_t D_k} \leq N_S</math> , | + | <math>\large\frac{H_S}{\Delta_t D_k}\normalsize \leq N_S</math> , |
where: | where: | ||
Line 187: | Line 187: | ||
Little information is available on the stability of the geosystems under overtopping currents. The equilibrium of forces on a single element suggests the following theoretical stability requirement: | Little information is available on the stability of the geosystems under overtopping currents. The equilibrium of forces on a single element suggests the following theoretical stability requirement: | ||
− | <math>\frac{u_{cr}}{\sqrt{g \Delta_t D_k}} \leq N_S</math> , | + | <math>\large\frac{u_{cr}}{\sqrt{g \Delta_t D_k}}\normalsize \leq N_S</math> , |
where: | where: | ||
Line 199: | Line 199: | ||
To determine the stability of geotextile bags and mattresses when subject to longitudinal current flows (current flow parallel to the structure), use can be made of the relation based on a fully protected foundation of sand (see, e.g., Pilarczyk<ref name="Pil"></ref>): | To determine the stability of geotextile bags and mattresses when subject to longitudinal current flows (current flow parallel to the structure), use can be made of the relation based on a fully protected foundation of sand (see, e.g., Pilarczyk<ref name="Pil"></ref>): | ||
− | <math>\Delta_t D_k \geq 0.035 \frac{\Phi K_T K_h u_{cr}^2}{2 g \Psi K_s}</math> , | + | <math>\Delta_t D_k \geq 0.035 \large\frac{\Phi K_T K_h u_{cr}^2}{2 g \Psi K_s}\normalsize </math> , |
where: | where: | ||
Line 205: | Line 205: | ||
<math>\Phi</math> is a stability parameter, with values of approximately 1.0 for a continuous top layer and 1.5 for edges; | <math>\Phi</math> is a stability parameter, with values of approximately 1.0 for a continuous top layer and 1.5 for edges; | ||
− | <math>\Psi</math> is the Shields parameter, <math>\Psi = \frac{\tau}{g D_k (\rho_s-\rho_w)} </math> , where <math>\tau</math> is the bed shear stress; | + | <math>\Psi</math> is the Shields parameter, <math>\Psi = \large\frac{\tau}{g D_k (\rho_s-\rho_w)} \normalsize </math> , where <math>\tau</math> is the bed shear stress; |
<math>K_T</math> is the turbulence factor, varying from 1.0 (for “normal” turbulence, as in rivers) to 2.0 (for strong turbulence) and higher (typically 3-4 for turbulence produced by propeller jets and other jets); | <math>K_T</math> is the turbulence factor, varying from 1.0 (for “normal” turbulence, as in rivers) to 2.0 (for strong turbulence) and higher (typically 3-4 for turbulence produced by propeller jets and other jets); | ||
Line 217: | Line 217: | ||
<math>Ks</math> is the slope factor, which is a function of the angle of shearing resistance between the geotextile element and the subsoil (<math>\delta</math>) and the slope angle of the structure (<math>\alpha</math>): | <math>Ks</math> is the slope factor, which is a function of the angle of shearing resistance between the geotextile element and the subsoil (<math>\delta</math>) and the slope angle of the structure (<math>\alpha</math>): | ||
− | <math>K_s = \sqrt{1-\frac{\sin^2 \alpha}{\sin^2 \delta}}</math> | + | <math>K_s = \sqrt{1-\large\frac{\sin^2 \alpha}{\sin^2 \delta}\normalsize }</math> |
For geotextile bags, internal sand movements are expected to occur under flow velocities higher than 1.5 m/s. When velocities are higher than 2.5 m/s bags, become unstable irrespective of size even when placed on slopes as low as 1V:8H. | For geotextile bags, internal sand movements are expected to occur under flow velocities higher than 1.5 m/s. When velocities are higher than 2.5 m/s bags, become unstable irrespective of size even when placed on slopes as low as 1V:8H. | ||
Line 242: | Line 242: | ||
Once the dimensioning of the sand-filled geosystems is completed, the geometric design shall be reviewed and the material and geotextile properties defined, from which a geotextile material can be selected and a definitive design determined. | Once the dimensioning of the sand-filled geosystems is completed, the geometric design shall be reviewed and the material and geotextile properties defined, from which a geotextile material can be selected and a definitive design determined. | ||
+ | |||
+ | |||
+ | ==Related articles== | ||
+ | :[[Artificial reefs]] | ||
+ | :[[Stability of rubble mound breakwaters and shore revetments]] | ||
==references== | ==references== | ||
− | |||
<references/> | <references/> | ||
Line 257: | Line 261: | ||
[[Category:Coastal protection]] | [[Category:Coastal protection]] | ||
[[Category:Hard structures]] | [[Category:Hard structures]] | ||
+ | [[Category:Soft coastal interventions]] |
Latest revision as of 16:31, 20 May 2020
Contents
Abstract
Sand-filled geosystems can be used in a wide range of coastal engineering applications. This article provides a summary of design rules based on the existing theories as well as recommendations regarding the durability and other properties of the materials used in the manufacturing of the geosystems. It is intended to give coastal managers, designers, contractors, and practitioners in general, insight in the applications and the limitations of sand-filled geosystems in coastal engineering and guide them forward to further reading in case more detail on their design is useful.
Introduction
Geosystems are three-dimensional elements manufactured from woven and/or non-woven geotextile fabrics. Even though there are a number of applications with open systems, e.g. the geotextile-wrap around revetment constructed at the Island of Sylt in Germany[1] , geosystem elements are generally pre-fabricated closed forms/units in four distinct types, bags, mattresses, tubes and containers. In special applications (e.g., dams), outside the scope of the present article, they can be made from water-tight geosynthetics, such as geomembranes and/or special composite systems. They can be filled with sand, gravel or mortar, yet only the use of sand as filling material is considered in this article.
Although the concept of wrapping sand in a geotextile is not innovative – actually it goes back to the 1950’s[2] – it was only in recent decades that attention has turned to the use of these materials on permanent coastal structures. Before they have been mostly applied on temporary and emergency works. Experience with sand-filled geosystems worldwide has shown that they can be used effectively as hidden components (e.g. in the core of a breakwater, groyne or seawall), in coastal areas exposed to low wave energy and/or tidal regime, on projects where there is no risk to life or assets in the event of failure, on projects with regular inspection and maintenance, and in complement to artificial sand nourishments. However, their wider application is still hampered by the lack of readily available knowledge. As a consequence, despite some recognised advantages, the use of sand-filled geosystems as alternative to more conventional materials (e.g., rock or concrete units) is seldom considered. Exceptions to such lack of knowledge are the books of Pilarczyk[3]] , which has the most thorough review of the knowledge and experience on geosynthetics and geosystems in coastal engineering from the late nineties of the last century and earlier and is still the reference book on this topic. Other references are
- Koerner[4] , which gives a general overview on designing with geosynthetics;
- the practice guideline on the application of geosynthetics in waterfront areas from PIANC[5];
- the translation into English and update of CUR-publication 217 “Ontwerpen met geotextiele zandelementen” by Bezuijen and Vastenburg[6] , which is currently the most comprehensive manual for designing with sand-filled geosystems;
- the recent past research at the Leichtweiss Institute in Germany (see, e.g., Dissanayake[7] ; Oumeraci and Recio[8] ; Recio[9] ; Oumeraci et al.[10] );
- DELTARES in The Netherlands (see, e.g., van Steeg and Vastenburg[11] ; and van Steeg and Breteler[12] );
- University of Porto in Portugal (see, e.g., das Neves et al.[13] ; and das Neves[14] ).
This article is based on the work presented in these references.
Definitions
For clarity, the following definitions apply in this article:
1. Geotextile tubes are water permeable, sand-tight geotextile (either woven, non-woven, or composite). They are delivered as prefabricated elements to the site, with a number of inlet/outlets for filling. The tube diameters can vary from about 1.6 to 5 m and the length may vary from 25 to 100 m depending on project specifics. When filled with sand or other granular materials the system acquires a pillow form. Geotextile tubes are typically suitable for applications above water and under water to about 6m water depth (i.e. emerged or submerged), and conveniently shall be hydraulically filled.
2. Geotextile containers are large geotextile (typically a woven material) elements containing from about 200 to 600 m3, which are dropped through water from a split barge (installation depth should allow for this). Containers are always installed submerged and can be used as core material of a breakwater that is covered with armour rock, or to raise the bed under the core of a breakwater. The container is unfolded in the split barge (so dimensions of the container have to be considered in relation with the barge dimensions) and the top is sewn in situ once the container is filled. Conveniently they shall be mechanically filled with dry clean sand; this is because it allows for a more even filling and for more air to be enclosed.
3. Geotextile bags are smaller containers manufactured from water permeable, sand-tight geotextile (either woven, non-woven, or composite) of about 0.3 to 10 m3 in volume. Bags can be installed emerged or submerged, possible applications are dune reinforcements, groynes, and offshore scour protections. Typically, they are mechanically filled.
4. Geotextile mattresses are cellular elements manufactured from water permeable, sand-tight geotextile (either woven or composite). Mattresses can be installed as slope or bottom protections. The choice of materials and filling procedure (mechanical or hydraulic filling) depends on project specifics.
General design aspects
Design approach
As presented by Bezuijen and Vastenburg[6], the design of sand-filled geosystems is an iterative process (see Figure 1), where various solutions that comply with functional and performance requirements are sought until a definitive design. Although most of the stages in the design process for sand-filled geosystem are comparable to any other construction material, there are some specifics to the use of such synthetic elements relating to (1) the mechanical (mainly the strength of the fabric and seams), hydraulic and durability properties of the fabric from which the geosystem is manufactured and its connections, (2) the execution methods and the availability of suitable filling material, (3) the impact of deformations on the hydraulic stability of elements and (4) the susceptibility of the materials to damage due to either poor installation, accidental occurrence or vandalism. For these specifics the design process for geosystems shall be made in consultation with manufacturers and installation contractors, with which the designer should closely interact.
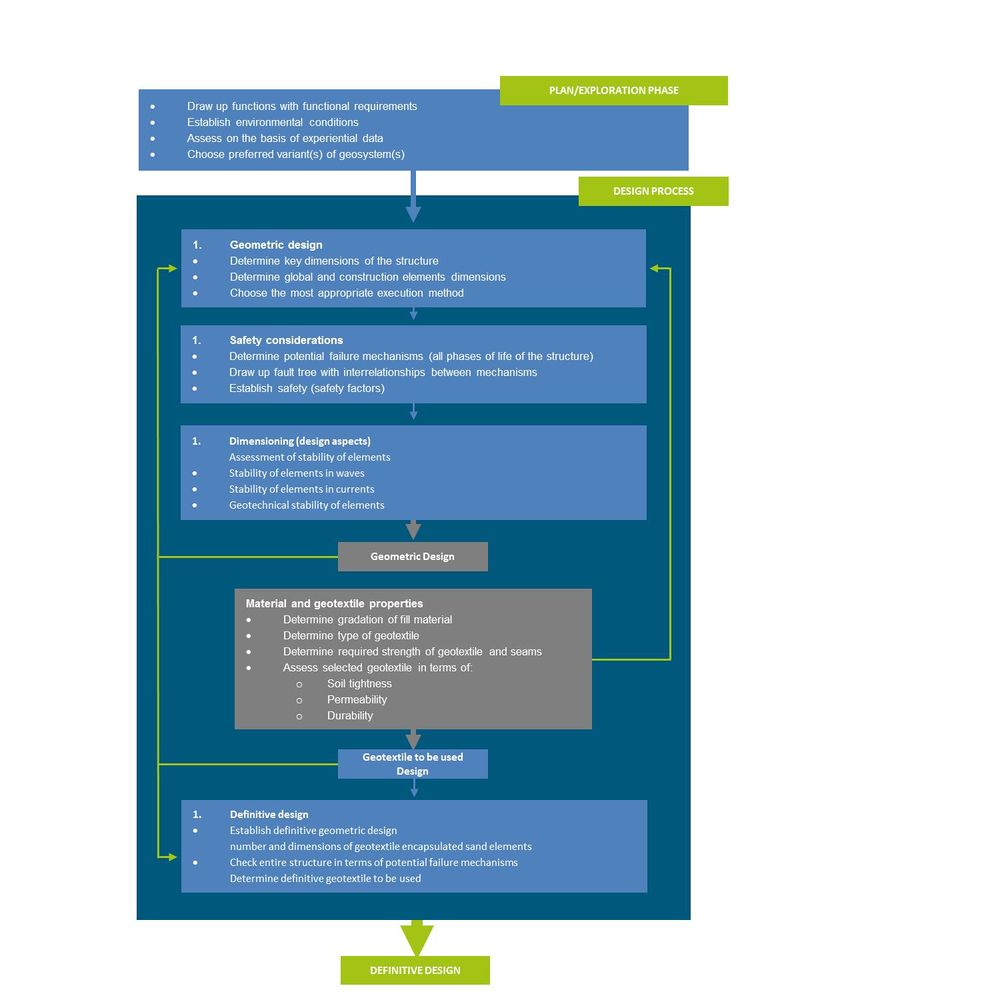
Potential failure mechanisms and safety considerations
Geotextile tubes
The following failure mechanisms shall be considered in the design of the geotextile tubes:
- Rupture of the geotextile through excessive pressure during filling;
- Rupture of the geotextile tube through inadequate strength of the seams;
- Instability (rolling) of the geotextile during filling;
- Instability of the geotextile tube under wave loading and/or water currents;
- Loss of stacking stability of the geotextile tube;
- Damage due to construction works;
- Damage to any surface finishing (for example during the installation of the armour layer);
- Sand migration within or from the geotextile tube;
- Draining of the retained material (subsoil/sand behind the geotextile tube);
- Foundation failure and deformation;
- Degradation of the geotextile (creep, UV radiation, abrasion, etc.);
- Accidental occurrence or vandalism.
Geotextile containers
The following failure mechanisms shall be considered in the design of the geotextile containers:
- Weakening/rupture of the geotextile and/or seams on the geotextile container leaving the split barge;
- Rupture of the geotextile and/or seams upon container impact on the bottom;
- Failure of the geotextile under the action of waves and/or currents;
- Loss of stacking stability of the geotextile containers;
- Damage due to construction works;
- Damage to any surface finishing (for example during the installation of the armour layer);
- Sand migration within or from the geotextile container;
- Foundation failure and deformation;
- Degradation of the geotextile (creep, UV radiation, abrasion, etc.).
Geotextile bags
The following failure mechanisms shall be considered in the design of the geotextile bags:
- Rupture of the geotextile bags during handling and placement;
- Insufficient seam strength;
- Instability of the geotextile bags under wave loading and/or water currents;
- Sand migration within or from the geotextile bags;
- Foundation failure and deformation;
- Liquefaction of the filling material (no danger if structure slope is milder than 1V:3H);
- Degradation of the geotextile (creep, UV radiation, abrasion, etc.);
- Accidental occurrence or vandalism.
Geotextile mattresses
The following failure mechanisms shall be considered in the design of the geotextile mattresses:
- Rupture of the geotextile mattresses during handling and placement;
- Rupture of the geotextile mattresses as a result of anchoring (e.g. due to additional loads);
- Insufficient seam strength;
- Instability of the geotextile mattresses under wave loading and/or water currents;
- Failure of the foundation;
- Liquefaction of the subsoil;
- Degradation of the geotextile (creep, UV radiation, abrasion, etc.);
- Accidental occurrence or vandalism.
Safety factors
In the design process a safety factor of 1.1 to 1.2 is recommended for geosystems in relation to the design value. Where relevant, additional safety factors (e.g. strength-reduction material factors) based on data provided by the manufacturer or derived from relevant publications (e.g., Koerner[4]) shall be taken into account. Examples of (commonly used) additional factors are: the strength-reduction material factors of seams (can vary from 30% to over 80% of the strength of the fabric depending on the strength efficiency of the seam, which means factors ranging from 3.33 to less than 1.2); the strength-reduction material factors for creep (a typical value for this factor is 1.4); and the strength-reduction material factors for abrasion (a typical value for this factor is 1.25). Overall safety factors greater than 5 can be justifiable depending on the execution methods and on aspects related to durability and life-performance.
Normative references and material aspects
Normative references
Table 1 includes the essential characteristics of geotextiles and geotextile-related products in coastal erosion when used for purposes of filtration, separation, and/or reinforcement, as per EN 13253 "Geotextiles and geotextile-related products – Required characteristics for use in erosion control works". Reference is made to the original documents for further detail on the scope of each of the standards included in Table 1.
Depending on the function(s) to be fulfilled by a geotextile in a certain application, prescriptions are made which (characteristic) properties of the geotextile (and value, where applicable) shall be included in the technical specifications for a work. These prescriptions will allow for a selection of suitable materials. However, it should be noted that some of the tests in Table 1 (for instance, the puncture and perforation tests) are performed according to a standard method, and therefore do not reflect specific circumstances in reality (for instance, an uncontrolled placement of rock on top of a geotextile fabric). This means that comparing products from different manufacturers with each other is not sufficient to assess performance. Hence, products should be judged on their in-situ based performance in past experiences, where possible.
Raw materials and processing
The following raw materials are used to produce the geotextiles from which geosystems are manufactured:
- polyester (PET);
- polypropylene (PP); and
- polyethylene (PE).
The processing technology consists of melting the polymers in granular form followed by extrusion, and eventually spinning. During the melting before extrusion and during further processing, additives can be used as a way to improve the less favourable properties of the basic materials. For instance, polyolefin materials such as polypropylene (PP) and polyethylene (PE) are inherently more sensitive to oxidation than those based on polyethylene terephthalate (PET); however, this behaviour can be improved very effectively by the use of appropriate stabilizing additives. Pigments can also be added. The final processing of the semi-manufactured products (e.g. yarns, filaments, tapes, etc.) will provide the end products (e.g., woven, non-woven or knitted geotextiles) with distinct characteristics. During the design it should be considered that some geotextile properties such as strength and elongation are derived from the basic materials (i.e., polymers) and from the final processing which yields the shape of the end product (which governs, e.g., permeability and soil tightness), while others such as creep are governed by the raw material only. As such, the use of PET polymers can prove advantageous for its better long-term load carrying capabilities if the geotextile will remain under tension in the structure.
The specific gravity is governed by the raw material. In this regard it is important to consider, most particularly during installation and before when selecting the execution method, that the polyolefin materials (PP and PE) are lighter than water (typically between 0.9 and 0.95) so materials will float, and that PET will sink in water. For filter or separation functions the geotextile has to be flexible, water-permeable and soil-tight; relevant properties are the aperture size and shape, and the permittivity. Yet, as very often the material has to fulfil several functions, it is possible that a geotextile with a filter function has to absorb tensile stresses. Soil reinforcement requests strong, relatively stiff and preferably water-permeable materials; critical properties are strength and stiffness, although deformations and puncture may have a great impact on the admissible stresses. Mechanical properties are important in those applications where the geotextile is required to perform a structural role. These properties are also very important when the geotextile is required to survive installation damage and localised stresses.
Material and geotextile properties
The material and geotextile properties that need to be defined during the design of a sand-filled geosystem are the gradation of the fill material, type of geotextile fabric from which the geosystem is manufactured and required tensile strength of geotextile and seams. In the following, selected geotextile fabrics are assessed in terms of soil tightness, permeability, and durability. The geotextile materials used in the manufacturing of geosystems are required to function as a geometrically closed filter (i.e., filter pores are so small that the sand is physically blocked), so to prevent the loss of the fill material over time through the geosystem for all hydraulic gradients while allowing relatively unrestricted water movements through it. The geotextile properties that govern particle retention and water passage capability are the characteristic opening size (or O90) and permeability normal to the plane (or kF), respectively.
The basic principle for determining the required characteristic opening size (O90) of the geotextile is that only a very limited amount of sand may be washed away, otherwise the sand-filled geosystem will deform excessively. It should be noted that when a geosystem is hydraulically filled, some loss of sand during the filling process is normally of no concern. Recommended design criteria for geometrically closed geotextile filters based on fill material properties and hydraulic load are presented in the books of Pilarczyk[3] and Bezuijen and Vastenburg[6].
The permeability of geotextiles in general, and thus also of geotextile-encapsulated sand elements in particular, has to be great enough to prevent the development of excessive pore pressures. A safe assumption is that the permeability of the geotextile must be at least 10 times that of the permeability of the fill material it is filtering. The geotextile fabric from which the geosystem is manufactured must be robust enough to avoid damage due to high stresses occurring especially during installation, as the filling and installation methods govern the required tensile strength of the geotextile used. In addition, the prescribed geotextile shall have an elongation at rupture that is sufficiently high to avoid damage due to high localised stresses. Depending on the application and execution method to determine the required tensile strength and strain of the geotextile, the raw material and its manufacturing process shall also be considered. For instance, woven geotextiles generally have a relatively high tensile strength and a low maximum strain, while nonwoven geotextiles have a relatively low tensile strength and a high maximum strain. A greater tensile stiffness can be an advantage if maintenance of shape is important, as a stiffer material will not deform as readily.
The strength efficiency of the seams made in the factory is normally a differentiating aspect between geosystems from different manufacturers. It should be noted that a very high reduction percentage in strength (or a very low strength efficiency of the seams) is always a waste in material, as the maximum allowable tensile load in the geosystem will be equal to the maximum tensile strength of the seam and not of the geotextile. For seams made on-site, by a hand sewing machine, lower strengths are normally obtained; therefore, they should be kept to a minimum.
Durability and life-performance
Under certain circumstances (e.g., UV-load, hydrolysis, and chemical and/or biological attack), and in the course of time (e.g., due to mechanical damage, fatigue, or creep), the properties of geotextiles can change unfavourably. Indeed much of the uncertainty with respect to geotextiles in civil engineering in general, and in coastal engineering in particular, is related to durability and life-time performance. It is a well-known fact that geotextile fabrics are very susceptible to weathering and must be protected against UV-light. There is a real concern about geotextiles, which links to their fragility against mechanical impact and vandalism.
The decay in resistance due to mechanical damage, weathering (most especially, raised temperature and ultraviolet radiation), chemical degradation, and biological degradation may result in the loss of performance, as a consequence of a loss in strength and in functioning. Differences between geotextile fabrics are very often related to the durability properties of the materials. However, because of the fact that some of the test results cannot be interpreted as a guarantee under normal conditions but rather a tool for selecting a product suitable for the anticipated working life, it is quintessential to judge products based on their performance in-situ.
The extent to which the material loses performance determines durability, which is also influenced by degradation processes during handling and in-service. The term durability is also applied to refer to the capability of the project to continue functioning at an acceptable level even after the construction material has begun to degrade. During application there is a great probability of mechanical damage. Also, storage and transport require special attention. Moreover, depending on the location and accessibility to the geotextiles, there is a risk of vandalism. All such factors may lead to a reduction in tensile strength, leakage, tearing, crack formation, plastic deformation and differential stretching. These factors are relevant because of the additional stresses or component failures they may induce and/or because of their effect in losing functionality.
Environmental conditions relevant to coastal engineering applications are the geotextiles’ exposure to sunlight (duration and intensity) both in-service and at installation. Raised temperature and ultraviolet radiation may have a negative effect on geotextiles because such ageing agents stimulate oxidation by which the molecular chains are cut off. Once this process starts, the molecular chains of the geotextile degrade continuously and the original molecular changes. Typically, when the geotextile is exposed to raised temperature and ultraviolet radiation for long time it becomes brittle and loses mechanical resistance. To reduce sensitivity to ageing, additives (e.g., anti-oxidising agents and UV-stabilisers) can be used as a way to improve the less favourable properties of the basic materials. For instance, carbon black is indispensable for extending the life-time expectancy of geotextile materials.
Conveniently, according to the life-time expectancy and the basic material, the chemical resistance (ISO 12960; ISO 13438; and ISO 12447) and microbiological resistance (ISO 12225) should be tested. For instance, some geosynthetics like nylon (polyamide) and, to a lesser extent, polyester are sensitive to hydrolysis under wet conditions (i.e., reaction to water). Moreover, reinforcing materials made of polyester are strongly attacked under high-alkaline conditions, whereas polypropylene can be attacked by some fungi.
Appendix B to standard ISO 13253 presents generic aspects of durability against harmful effects. It provides guidance on maximum exposure times according to the application and the residual resistance after accelerated-ageing test (ISO 12224), and establishes thresholds of resistance in regard to the raw material.
Finally, one aspect that is not often seen in many publications (although mentioned in standard ISO 13253) but should be carefully considered, is the use of recycled polymers in the fabrication of geotextiles, as it can significantly affect its durability and life-performance.
Hydraulic design criteria for sand-filled geosystems
Stability under wave loading
Several research results suggest that the hydraulic stability of sand-filled geosystems can be checked by means of the following equation:
[math]\large\frac{H_S}{\Delta_t D_k}\normalsize \leq N_S[/math] ,
where:
[math]N_S[/math] is the stability parameter, a number typically ranging between 0.5 and 3;
[math]H_S[/math] is the significant wave-height [m];
[math]D_k[/math] is the effective thickness of the geosystem element [m], which depends on the dimensions of the geosystem and how it is placed with respect to the incident wave direction.
[math]\Delta_t[/math] is the relative density of the structural elements, which can be calculated from
[math]\Delta_t = (1-n) (\rho_s - \rho_w)/\rho_w[/math] , where [math]\rho_s[/math] is the density of the sediment fill [kg/m3], [math]\rho_w[/math] is the water density [kg/m3] , [math]n[/math] is the porosity of the geosystem fill material.
The stability parameter [math]N_S[/math] is expected to depend on an empirical coefficient, which accounts for several factors including the position of the elements with relation to still water level, structure slope, friction, degree of filling, shape and deformation of the elements, and on the breaker parameter, thus accounting for the incident wave period. Based on existing research, Bezuijen and Vastenburg[6] present the stability parameters that can be used for the preliminary design of geotextile tubes, containers, bags and mattresses. With respect to geotextile mattresses their use is not recommended where the significant wave height is greater than 1.0 m.
Stability under water currents
Little information is available on the stability of the geosystems under overtopping currents. The equilibrium of forces on a single element suggests the following theoretical stability requirement:
[math]\large\frac{u_{cr}}{\sqrt{g \Delta_t D_k}}\normalsize \leq N_S[/math] ,
where:
[math]N_{S}[/math] is the stability parameter, typically ranging between 0.5 and 1.8 (0.5 to 1.0 are recommended values for preliminary design);
[math]u_{cr}[/math] is the critical flow velocity [m/s];
[math]g[/math] is the acceleration due to gravity.
To determine the stability of geotextile bags and mattresses when subject to longitudinal current flows (current flow parallel to the structure), use can be made of the relation based on a fully protected foundation of sand (see, e.g., Pilarczyk[3]):
[math]\Delta_t D_k \geq 0.035 \large\frac{\Phi K_T K_h u_{cr}^2}{2 g \Psi K_s}\normalsize [/math] ,
where:
[math]\Phi[/math] is a stability parameter, with values of approximately 1.0 for a continuous top layer and 1.5 for edges;
[math]\Psi[/math] is the Shields parameter, [math]\Psi = \large\frac{\tau}{g D_k (\rho_s-\rho_w)} \normalsize [/math] , where [math]\tau[/math] is the bed shear stress;
[math]K_T[/math] is the turbulence factor, varying from 1.0 (for “normal” turbulence, as in rivers) to 2.0 (for strong turbulence) and higher (typically 3-4 for turbulence produced by propeller jets and other jets);
[math]K_h[/math] is the depth factor, used for translation of the depth average flow velocity into a flow velocity at any depth ([math]h[/math]) along the structure. For a fully developed current profile
[math]K_h=2/(log(12h/k_r))^2[/math] , where [math]k_{r}[/math] is the equivalent roughness according to Nikuradse (assumed equal to [math]D_{k}[/math]) and [math]h[/math] the flow depth;
for an undeveloped current profile [math] K_{h}=(h/k_{r})^{{-0.2}}[/math] and for a very rough current [math]K_h \approx 1 [/math] ;
[math]Ks[/math] is the slope factor, which is a function of the angle of shearing resistance between the geotextile element and the subsoil ([math]\delta[/math]) and the slope angle of the structure ([math]\alpha[/math]):
[math]K_s = \sqrt{1-\large\frac{\sin^2 \alpha}{\sin^2 \delta}\normalsize }[/math]
For geotextile bags, internal sand movements are expected to occur under flow velocities higher than 1.5 m/s. When velocities are higher than 2.5 m/s bags, become unstable irrespective of size even when placed on slopes as low as 1V:8H.
Scour development around sand-filled geosystems
There is very little information on scour development around sand filled geosystems, with the exception of research results based on a series of laboratory measurements of the hydrodynamic and morphodynamic change produced in the vicinity of sand-filled geosystem structures under wave loading at UPorto in Portugal (see, e.g., das Neves et al.[13]; and das Neves[14]).These research results indicate that:
- Scour development is likely dominated by mechanisms of wave reflection off the structure and wave downrush flow on the exposed slope. The geometric characteristics of the structures (e.g., shape of elements, and porosity) also seem to influence scour development namely due to their effect on those two aspects (i.e., wave reflection, and downrush);
- The comparison of the measured scour depth to the scour depth calculated from predictors has shown that these predictors completely underestimated scour for structures placed landward of the shoreline and for structures exposed to wave breaking of increased intensity due to shoreline retreat. It further showed, that scour depth tends to be less than the incident unbroken wave-height.
Final remarks
In this article we have considered only the hydraulic design of geosystem elements and not the geotechnical stability of the full structure. Some stability aspects, internal sand movement and liquefaction, are mentioned below. The reader may consult Bezuijen and Vastenburg[2] and references cited therein for details on the geotechnical design of sand-filled geosystems. The stability of a mound (or stack) structure of geosystem elements is dependent on the following potential failure mechanisms:
- stability of the mound under wave loading;
- shear failure of the subsoil; and
- liquefaction of the subsoil.
If the structure is formed as a mound (or stack), pressure differences may occur between the water pressure within the mound (or stack) and the external water pressure. This may cause shearing failures in part of the mound (or stack) and thus pose a threat to stability. There is generally little information available on this, with the exceptions of some work done in Leichtweiss Institute in Germany and DELTARES in The Netherlands.
Excessive deformation due to internal sand movement inside elements may also cause the structure or the elements to become unstable. Excessive deformation depends on hydraulic load and degree of filling, but there is generally little information available on this with the exceptions of some work done in Leichtweiss Institute in Germany and DELTARES in The Netherlands.
Liquefaction refers to the loss of shear resistance in saturated, cohesionless soils during dynamic loading or during earthquakes. Liquefaction may also occur in loose, fine marine soils under wave-loading. With regard to the latter occurrence for structures with reasonably well-compacted sandy subsoil, there is no danger of liquefaction if the slope is less than or equal to 1V:3H, according to Bezuijen and Vastenburg[2].
Once the dimensioning of the sand-filled geosystems is completed, the geometric design shall be reviewed and the material and geotextile properties defined, from which a geotextile material can be selected and a definitive design determined.
Related articles
references
- ↑ Nickels, H.; and Heerten, G. (1996). Building elements made of geosynthetics and sand resist North Sea surf. Proceedings of the First European Geosynthetic Conference (EuroGeo), Maastricht, The Netherlands, October 1996.
- ↑ 2.0 2.1 2.2 Bezuijen, A.; and Vastenburg, E. (2008). Geosystems, possibilities and limitations for applications,Proceedings of EuroGeo4: Fourth European Geosynthetics Conference, Edinburgh, Scotland, United Kingdom.
- ↑ 3.0 3.1 3.2 Pilarczyk, K. (2000). Geosynthetics and geosystems in hydraulics and coastal engineering, Rotterdam: A.A.Balkema Publications, 913p, ISBN 90-5809-302-6.
- ↑ 4.0 4.1 Koerner, Robert M. (2006). Designing with geosynthetics, Xlibris Corp., 524pp, ISBN-13: 978-1462882885.
- ↑ PIANC (2011). The application of geosynthetics in waterfront areas, PIANC Report no. 113.
- ↑ 6.0 6.1 6.2 6.3 6.4 Bezuijen, A.; and Vastenburg, E.W., 2013. Geosystems Design Rules and Applications, CRC Press, 145pp, ISBN 978-0-415-62148-9.
- ↑ Dissanayake, D.T. (2013). Experimental and Numerical Modelling of the Hydraulic Stability of Geotextile Sand Containers for Coastal Protection, PhD Thesis: Leichtweiβ Institute for Hydraulic Engineering and Water Resources, Germany.
- ↑ Oumeraci, H.; and Recio, J. (2009). Geotextile sand containers for shore protection, Handbook of Coastal and Ocean Engineering, Y.C. Kim (ed.), Singapore: World Scientific Publishing Co. Pte. Ltd., pp. 553-600, ISBN 13-978-981-281-929-1.
- ↑ Recio, J. (2007). Hydraulic stability of geotextile sand containers for coastal structures - effect of deformations and stability formulae, PhD Thesis: Leichtweiβ Institute for Hydraulic Engineering and Water Resources, Germany.
- ↑ Oumeraci, H.; Hinz, M.; Bleck, M.; and Kübler, S. (2002). Großmaßstäbliche Untersuchungen zur hydraulischen Stabilität geotextiler Sandcontainer unter Wellenbelastung, Braunschweig, Germany: Leichtweiβ Institute for Hydraulic Engineering and Water Resources, Research Report no. 878, unpublished (in German).
- ↑ van Steeg, P.; and Vastenburg, E. (2010). Large scale physical model tests on the stability of geotextile tubes, DELTARES.
- ↑ van Steeg, P.; and Breteler, K. (2008). Large scale physical model tests on the stability of geocontainers, DELTARES.
- ↑ 13.0 13.1 das Neves, L.; Moreira, A.; Taveira-Pinto, F.; Lopes, M.L.; and Veloso-Gomes, F. (2015). Performance of submerged nearshore sand-filled geosystems for coastal protection. Coastal Engineering 95, 147–159, doi:10.1016/j.coastaleng.2014.10.005.
- ↑ 14.0 14.1 das Neves, L. (2011). Experimental stability analysis of geotextile encapsulated-sand systems under wave-loading (Ph.D. thesis), University of Porto.